Contents
- 1 VDA 6-3 | VDA 6.3 Process Audit [2024] | VDA 6.3 Full Form
- 2 What is VDA 6.3? VDA 6-3?
- 3 Who Developed VDA 6.3?
- 4 Phases of VDA 6.3 or Process Elements of VDA6.3 or VDA Audit
- 5 VDA 6.3 Process Audit Questionnaire Overview
- 5.1 Phase 2 (P2), Project Management
- 5.2 Phase 3 (P3), Planning of Product & Process Development
- 5.3 Phase 4 (P4), Carrying Out Product & Process Development
- 5.4 Phase 5 (P5), Supplier Management
- 5.5 Phase 6 (P6), Process Analysis & Production Control
- 5.6 Phase 7 (P7), Customer Support / Customer Satisfaction / Service
- 6 VDA 6.3 Process Audit Checklist (vda6.3 or vda audit)
VDA 6-3 | VDA 6.3 Process Audit [2024] | VDA 6.3 Full Form
With today’s innovation and technology in manufacturing industries ensuring the product quality is very much essential, especially when there are any concerns. Such concerns or problems can be solved with the help of 8D problem solving tool or A3 sheet or 5 why analysis there by implementing permanent corrective actions.
Ensuring compliance and conformance in any manufacturing industry requires regular audits. One such most effective in-depth manufacturing audit tool is called VDA 6-3 Process Audit or VDA 6.3 Process Audit.
The VDA 6.3 Standard is now considered to be one of the most preferred or used manufacturing process audit tool which helps you find all kinds of gaps throughout the organization, especially in manufacturing lines or production areas which helps to close the gaps with proper robust corrective actions.
The VDA 6.3 process audit tool is mostly used in automotive industries, especially when the customers are directly or indirectly from Germany.
What is VDA 6.3? VDA 6-3?
What is VDA 6.3?
VDA 6.3 full form stands for “Verband Der Deutschen Automobilindustrie”. VDA 6.3 is one of the excellent tools for in-depth manufacturing process audits within the automotive industry which acts as a guideline for performing audits.
Download VDA 6.3 Standard: VDA 6.3 pdf
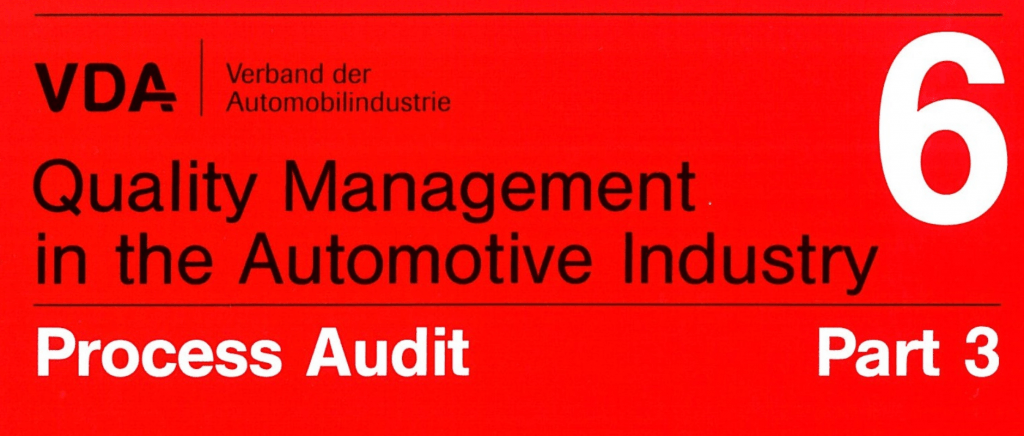
In other words, the VDA 6.3 is a quality management system standard which is must have certification or must have audit score or mandatory for German car makers. However, the standard can actually be applied to other businesses, such as manufacturing, automotive suppliers or FMCG environments.
VDA 6.3 provides information on the significance and application scope of a process audit over the entire product realization cycle starting from planning phase till customer feedback phase in both manufacturing and services.
VDA 6.3 process audit tool defines the audit phases, audit process, the criteria for evaluation of the process audit, audit results and the requirements of the processes.
VDA 6.3 is an “in-depth” manufacturing process audit tool.
VDA 6.3 means, the German trade association for the automotive industry is known by the initials VDA (Verband Der Deutschen Automobilindustrie E.V.).
The VDA 6.3 is developed by VDA QMC and the German automotive industry, where-in the VDA 6.3 defines a process-based audit standard for evaluating and improving controls and fixing the gaps in a manufacturing organization’s processes.
The complete VDA 6.3 standard and its each step in the process in the form of phases is modelled with six links which is governed by the “Deming’s Loop called Plan, Do, Check and Act”.
Who Developed VDA 6.3?
The VDA 6.3 is developed by VDA-QMC and most of the German automotive industries.
Later many OEM’s got involved and registered in the development and in publications of VDA 6.3 such as Opel, Audi, Benteler, BMW, BorgWarner, Continental, Daimler, Harman, Man, Knorr-Bremse, Magna, Otto Fuchs, Porsche, Bosch, Rollax, Schaffler, Volkswagen, ZF Friedrichshafen and so on.
The VDA 6.3 is an extension of ISO 9001:2015 + IATF 16949:2016 which aims to help automotive companies meet growth, innovation and compliance goals.
VDA 6.3 is one of the parts of the VDA family of documents. vda 6.3 focuses on in-depth manufacturing process audits for production parts, serial production and services, whereas the VDA 6.5 is a product audit and VDA 6.1 is a system audit.
· System Audit: IATF 16949:2016 / VDA 6.1 which aims to verify the overall effectiveness of the quality management system
· Process Audit: VDA 6.3 which aims to verify the effectiveness of the product realization processes
· Product Audit: VDA 6.5 which aims to verify the product conformance and compliance with respect to the defined specification throughout the manufacturing and dispatch processes
Phases of VDA 6.3 or Process Elements of VDA6.3 or VDA Audit
There are 7 phases in VDA 6.3. All the phases are divided based on covering all aspects and entities of an organization in order to ensure smooth manufacturing operation and fix the gaps in the manufacturing processes.
Phases of VDA 6.3 (VDA6 3 2016):
1. P1 = Potential Analysis
2. P2 = Project Management
3. P3 = Planning of Product & Process Development
4. P4 = Carrying Out Product & Process Development
5. P5 = Supplier Management
6. P6 = Process Analysis & Production Control
7. P7 = Customer Feedback / Support/ Customer Satisfaction/ Service
The P6 phase again divided into 6 sub-phases and are named as follows:
1. P6.1 = What goes into Process? (Process Input)
2. P6.2 = Work Content/ Process Sequence
3. P6.3 = Process Support/ Personal Resources
4. P6.4 = Material Resources
5. P6.5 = Process Effectiveness
6. P6.6 = What should Process Produce? (Process Output/ Process Result)
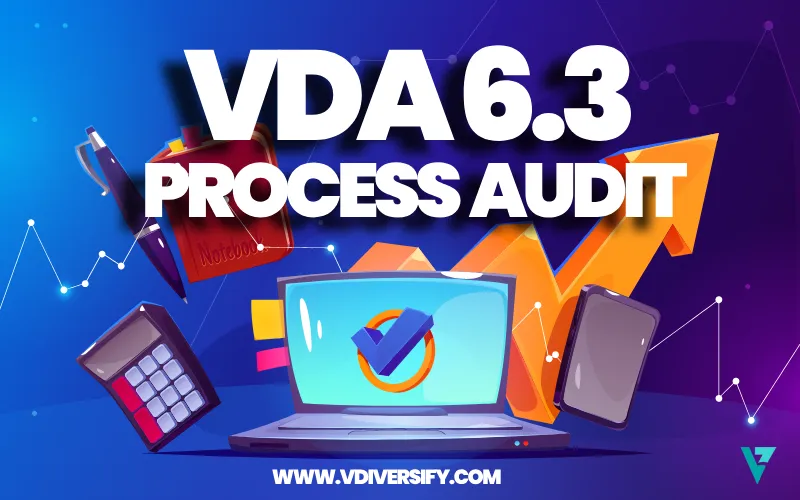
Potential Analysis (P1)
A potential analysis is used to evaluate new suppliers (contenders). For existing suppliers, the potential analysis can be used at new locations, with the introduction of new technologies or for new products.
Evaluation of a Potential Analysis:
The assessment is marked, using the traffic light system of “Red”, “Yellow” or “Green” (see below).
Adding the marks for each question results in an Overall Classification (see below).
Interpretation of Results:
Green = Fully Approved Potential Supplier
This means, a contract award or nomination for the project, component or product group by the customer is possible without restrictions.
Yellow = Conditionally Approved Supplier
This means, the supplier is able to meet the customer requirements for the questioned product scope and can be considered when awarding the contract.
Only a conditional approval for a contract award can be given. In some cases, the supplier needs support from the client to implement the requirements of the project. Under certain conditions a limited approval for a contract may be given (quantity reduction, smaller series….).
An award or nomination is possible, but is linked to defined conditions:
The conditions to minimize the risk may be:
· Restriction to a defined quantity (small-scale production)
· Restriction to a defined product
· Restriction to part-quantities of the overall enquiry
· The (potential) supplier receives a trial order on probation
· The (potential) supplier is included in a supplier development programme
· Special support from supplier development teams with careful monitoring of the progress of the project
Note: Conditions must be specified between the relevant quality and procurement departments.
Red = The (Potential) Supplier is Barred
This means, it is not possible to award (nominate the company for) the project, component or product group in question.
A positively evaluated potential analysis (“Green”, “Yellow”) is not necessarily coupled to an award of contract. A negatively evaluated potential analysis (“Red”) excludes a contract award.
Evaluating a Process Audit for Material Products: Evaluation of The Individual Questions:
Each question is assessed in terms of compliance with the requirements and the risk involved. The assessment of each question can result in the award of 0, 4, 6, 8 or 10 points, with the number of points awarded being based on proven compliance with the requirements.
**) The term “mainly” means that the relevant requirements are met in most instances and no special Risks have been identified.
Questions involving Special Product and Process Risk (* Question):
In the process elements, questions involving special risks in terms of product & process are identified by an asterisk (*).
The specific risks in the * Questions are already taken into account by the classification rules. The evaluation is carried out analogously to the remaining questions, this means, * Questions are not evaluated more severely than other questions.
Overall Level of Compliance:
Note: Sub-Elements of P6: In the process element P6 the following sub-elements are evaluated.
Overall Compliance: VDA 6.3 (VDA6 3 2016) Scoring System
Partial Audits can also be conducted and Compliance is done as below:
Example P5/P6/P7:
If the process elements P5, P6, P7 are evaluated (e.g., auditing of serial production) then the result is calculated as follows:
Example P4:
If only process element P4 is evaluated (e.g., audit at the time of handing over the project to serial production) then the result is calculated as follows:
The designation EGP(P5P6P7) and EGP(P4) are used to easily identify of the process elements evaluated.
To classify the compliance of a partial audit the calculated compliance (e.g., EGP(P5P6P7) and EGP(P4) is compared to the benchmarks as given above (at least 80% for a “B” classification of conditionally quality capable or at least 90% for quality capable).
Rules for Downgrading:
The following rules for downgrading are to be used and documented in the audit report:
1. Reasons for downgrading from A to B even though the level of achievement is EG or EG(Pn) ≥ 90%:
· At least one process element (P2 to P7) or process step (E1 to En) is evaluated with a level of achievement EG or EG(Pn) or En from < 80%
· A level of achievement in one of the sub-elements of P6 is < 80%
· At least one *-question is rated with 4 points
· At least one question from the Process audit is rated with 0 points
2. Reasons for the downgrading to C even though the level of achievement is EG or EG(Pn) ≥ 80%:
· At least one process element (P2 to P7) or process step (E1 to En) is evaluated with a level of achievement EG or EG(Pn) or En from < 70%
3. Reasons for the downgrading to C even though the level of achievement is EG or EG(Pn) ≥ 80%:
· A level of achievement EU1 to EU7 in one of the sub-elements of P6 is < 70%
· At least one *- question is rated with 0 points
The overall result is rounded to the nearest percentage point. Similarly, when applying the downgrading rules (process element, sub-element or process step), the individually calculated results EPn, EUn are rounded to the nearest percentage point.
VDA 6.3 Process Audit Questionnaire Overview
The below table shows the overview of the VDA 6.3 process audit questionnaire or VDA 6.3 process audit potential analysis checklist. This is the ultimate vda 6.3 process audit checklist you must understand if you want to become a VDA auditor.
Phase 2 (P2), Project Management
Potential Analysis**
P2
Project Management
2.1
Is Project Management established with a project organization?
X
2.2
Are all resources required for the project development planned and available and are changes shown?
X
2.3
Is there a project plan and has this been coordinated with the customer?
X
2.4
Is the advanced product quality planning implemented within the project and monitored for compliance?
X
2.5*
Are the procurement activities of the project implemented and monitored for compliance?
X
2.6*
Is change management within the project ensured by the project organization?
X
2.7
Is there an escalation process established and is this effectively implemented?
X
Phase 3 (P3), Planning of Product & Process Development
Potential Analysis**
P3
Planning of Product & Process Development
3.1
Are the specific product and process requirements available?
X
3.2*
Can the manufacturing feasibility be evaluated according to the product and process requirements?*
X
3.3
Are the activities for the product and process development planned in detail?
3.4
Are the activities for customer support / customer satisfaction / customer service planned?
3.5
Have the necessary resources been taken into account for the product and process development?
Phase 4 (P4), Carrying Out Product & Process Development
Potential Analysis**
P4
Carrying Out Product & Process Development
4.1*
Are the actions which were defined in the product and process development phases implemented?
X
4.2
Are human resources available and are they qualified to ensure the start of the series?
4.3
Are the material resources available and suitable to ensure the start of the series?
X
4.4*
Are the required approvals and releases for the product and process development available?*
X
4.5
Are the manufacturing and inspection specifications derived from the product and process development and are they implemented?
4.6
Is a performance test carried out under series conditions for the series release?
4.7*
Is there a controlled method for the product handover from development to serial production?
Phase 5 (P5), Supplier Management
Potential Analysis**
P5
Supplier Management
5.1
Are only approved and quality-capable suppliers used?
X
5.2
Are customer requirements taken into account in the supply chain?
X
5.3
Have target agreements for supplier performance been agreed upon and implemented?
5.4*
Are the necessary releases available for out-sourced products and services?
X
5.5*
Is the quality of the out-sourced products and services ensured?
X
5.6
Are incoming goods stored appropriately?
X
5.7
Are personnel qualified for their respective tasks and are responsibilities defined?
Phase 6 (P6), Process Analysis & Production Control
Potential Analysis**
P5
Process Analysis & Production Control
6.1
What goes into Process? (Process Input)
6.1.1
Has the project been transferred from development to serial production and is a reliable start guaranteed?
X
6.1.2
Are the necessary quantities / production batch sizes of incoming materials available at the agreed upon time and at the right location (storage / work- station)?
6.1.3
Are incoming materials stored appropriately and are the means of transport / packing facilities suitable for the special characteristics of the incoming materials?
6.1.4
Are the necessary identifications / records / releases available and allocated appropriately to the in- coming materials?
6.1.5*
Are changes to the product or process made during the serial production tracked and documented?
Potential Analysis**
P6
Process Analysis & Production Control
6.2
Work Content/ Process Sequence
6.2.1
Are the specification of the control plan complete and have they been effectively implemented?
X
6.2.2*
Is there a restart of production of manufacturing processes?
X
6.2.3*
Are special characteristics managed in the production?
X
6.2.4*
Are non-released and / or defective parts managed?
X
6.2.5
Is the flow of materials and parts secured against mixing / wrong items?
Potential Analysis**
P6
Process Analysis & Production Control
6.3
Process Support/ Personal Resources
6.3.1*
Are the employees able to fulfil their given tasks?
X
6.3.2
Do the employees know their responsibilities and authority in the monitoring of the quality of product and process quality?
6.3.3
Are the necessary personnel resources available?
X
Potential Analysis**
P6
Process Analysis & Production Control
6.4
Material Resources
6.4.1*
Can the product-specific requirements from the customer be met with the manufacturing equipment?
X
6.4.2
Is the maintenance of the manufacturing equipment and tools controlled?
X
6.4.3*
Can the quality requirements be effectively monitored with the measurement and testing facilities in use?
X
6.4.4
Are the work and inspection stations appropriate for the needs?
X
6.4.5
Are tools, equipment and testing equipment stored properly?
Potential Analysis**
P6
Process Analysis & Production Control
6.5
Process Effectiveness
6.5.1
Are there targets set for the manufacturing process?
6.5.2
Is quality and process data collected in a way that allows analysis?
6.5.3
In the case of deviations from product and process requirements, are the causes analyzed and the corrective actions checked for effectiveness?
X
6.5.4
Are processes and products audited regularly?
X
Potential Analysis**
P6
Process Analysis & Production Control
6.6
What should Process Produce? (Process Output/ Process Result)
6.6.1
Do the quantities / production batch sizes match needs and are they systematically directed to the next process step?
6.6.2
Are products / components stored in an appropriate manner and are transport facilities / packing arrangements suitable for the special characteristics of the products / components?
X
6.6.3
Are the necessary records / releases documented?
6.6.4*
Are customer requirements met at the delivery of the final product?
X
Phase 7 (P7), Customer Support / Customer Satisfaction / Service
Potential Analysis**
P7
Customer Support/ Customer Satisfaction/ Service
7.1
Are all requirements related to QM-System, product and process fulfilled?
X
7.2
Is customer service guaranteed?
X
7.3*
Is the supply of parts guaranteed?
X
7.4*
If there are deviations from quality requirements, are failure analyses carried out and corrective actions implemented effectively?
X
7.5
Are personnel qualified for the various tasks and are responsibilities defined?
Note:
- Highlighted Marking indicates: * – Questions
- ** Questions from the questionnaire that must be audited at a minimum within the framework of the potential analysis.
VDA 6.3 Process Audit Checklist (vda6.3 or vda audit)
The below is the (vad6 3 2016) VDA 6.3 pdf process audit checksheet. If you want to become a VDA auditor, then you must go through the VDA 6.3 process audit checklist as mentioned below:
Understanding VDA 6.3 process audits training:
Project Management (P2)
P2.1 | Is a Project Management established with a Project Organization?
Minimum Requirements relevant for Assessment
Examples for Implementation
A process for project management exists:
- The project organization is specified and contacts are defined.
- The responsibilities and authority of the project leader and team members are defined.
- The team members of the project are qualified to carry out their tasks.
- The project organization meets the customer requirements.
- Suppliers are involved in project management.
Defined roles, tasks, competence and responsibilities of the project leader / project team expert for technology:
- Project interface in multi-site projects
- Project organizational chart
- Composition of the project team
- Verification of qualifications
- Special customer requirements for project management
Project Management (P2)
P2.2 | Are all resources required for the project development planned and available and are changes shown?
Minimum Requirements relevant for Assessment
Examples for Implementation
Resource planning takes account of the customer’s requirements, based on the contract covering the project:
- Resource planning for project members is established and implemented. The staff workload has to be considered.
- Review and where necessary adjustment of resource planning is carried out when changes occur (dates, scope of development performance…). This applies to changes that are triggered by the customer as well as internal changes or supplier changes.
- The critical path is given special consideration within the resource planning.
- The necessary project budget for personnel and equipment (testing and laboratory equipment e.g.) is planned and released.
- Changes in the project organization (interface with client) are reported.
Evidence of resource planning (taking other projects into account):
- Resource planning for equipment (e.g., development test stand)
Project Management (P2)
P2.3 | Is there a project plan and has this been coordinated with the customer?
Minimum Requirements relevant for Assessment
Examples for Implementation
The project plan meets the specific customer requirements:
- All internal and customer defined milestones are fully incorporated in the project plan.
- A review is carried out at the milestones defined in the project plan to check that all planned activities are carried out and that the level of maturity required is achieved.
- If a statutory authorisation procedure for a product is specifically required, the duration of this procedure is included in the project planning.
- In-house communication is ensured when changes are made to the project plan. Changes made to the project plan which affect the customer are coordinated with the customer.
- The critical path is generated from the project plan and takes account of critical delivery items.
- The project plan must include the advanced product quality planning activities. This may be in a separate document that is referred to from the project plan.
- The plans must take prototype and pre-production into account.
- The project plan must include detailed activities for product and process development. Detailed plans may be in a separate document referred to in the project plan. The plans must take prototype and pre- production into account.
- The project plan must include the detailed activities concerning procurement. Detailed plans may be in a separate document referred to in the project plan.
Project plan with milestones:
- Specific customer requirements regarding technologies and/or product groups
- Customer’s project plan
- Customer’s deadlines
- Customer’s milestones
- Customer’s targets (measurements within the individual milestones)
- Milestone assessments (re- views)
- Quality Plan (e.g., from VDA MLA or APQP)
- Country specific certification requirements (ECE, SAE, DOT, CCC, …)
- Legal and Regulatory approvals process of critical systems (electroplating, paint, …)
Project Management (P2)
P2.4 | Is the advanced product quality planning implemented within the project and monitored for compliance?
Minimum Requirements relevant for Assessment
Examples for Implementation
The advanced product quality planning meets the specific customer requirements:
- Both product and process assurance measures are included as part of the advanced product quality planning.
- Verification and validation of the product and pro- cess requirements are contained within the planning.
- The planning also addresses critical components and scope of supply (internal and external suppliers).
- The plan is regularly monitored for compliance and for target achievement.
Project plan:
- Customer milestones
- Customer requirements in regard to quality plans
- Customer specifications
Project Management (P2)
P2.5* | Are the procurement activities of the project implemented and monitored for compliance?
Minimum Requirements relevant for Assessment
Examples for Implementation
The activities have to ensure that only approved and quality-capable suppliers are used in production:
- The level of activity depends on the risk classification of procured scope of supplies.
- These include the supplier selection and award criteria, award amount and delivery target date. The transfer of customer requirements in the supply chain is ensured.
- The activities also include client’s required suppliers as stated within the agreement.
- The suppliers for facilities, machinery, tools, test and measurement systems and services are integrated.
- The appointment of suppliers must be appropriately documented and traceable.
- Dates for the assignment, supplier milestones and release have been laid down in the plan and coordinated with the overall schedule.
Make or buy decisions:
- Supplier selection criteria
- Supplier development plan
- List of suppliers for the project
- List of approved suppliers
- Risk appraisal of each sup- plier
- Interface agreement for directed suppliers
- Component classification
- Suppliers of services such as development, laboratories and maintenance etc.
Project Management (P2)
P2.6* | Is change management within the project ensured by the project organization?
Minimum Requirements relevant for Assessment
Examples for Implementation
Change management within the project meets the customer’s specific requirements:
- Changes (initiated by the customer, in-house or by the client) must be evaluated and if necessary, the project plan must be adapted. This evaluation must include the risk assessment for the product quality as well as the deadlines.
- Suppliers (critical supplies) are actively involved in change management.
- Changes are reported in a timely manner and are agreed upon with the customer.
- Compliance must be ensured at change stop points. If deviations from this occur, they must be documented between the client and the supplier.
- All changes must be documented.
- The persons responsible for change management are defined for the client, in-house and to suppliers.
Time schedules:
- Process description
- Change management
- Change forms
- Change history for the product and the process
- Evaluation of change
- Approvals of changes
Project Management (P2)
P2.7 | Is there an escalation process established and is this effectively implemented?
Minimum Requirements relevant for Assessment
Examples for Implementation
The escalation process in the project meets the specific client requirements:
- An escalation model (risk management) must be available for deviations in the project affecting the overall schedule. Project risks are identified, assessed and reduced through measures applied to the product group concerned in each case.
- The criteria for escalation are defined, responsibilities and authorities are regulated and measures are taken when deviations occur.
- If risks have been identified in technologies, suppliers or supplier countries, these risks should be considered within the escalation management.
Time periods for escalation depending on the risk have been agreed upon:
- Contact personnel/ decision makers in the escalation process are defined.
- Escalation criteria and paths of communication are defined.
- Protocols of milestone re- views including measures
Planning of Product & Process Development (P3)
P3.1 | Are the specific product and process requirements available?
Minimum Requirements relevant for Assessment
Examples for Implementation
All requirements regarding the product to be developed are known:
- For products with integrated software, the requirements at interfaces between hardware and software are defined. Requirement management is implemented for this.
- The organisation must determine the logistical requirements and the statutory and regulatory requirements relevant for the product that are necessary to meet specific client requirements.
- The organisation must take into account and use requirements on the product and the process known from previous experience.
- Special characteristics must be identified on the basis of their own requirements, customer requirements, legal requirements, manufacturing technology and characteristics that arise from the purpose / use of the product.
- The quality requirements from the client for the product and the process must be available.
- Inquiry and contract documents are checked for completeness.
- If customer requirements cannot be fulfilled the customer must be notified or deviations “allowed” / approved from the customer (if the contract has been awarded).
- Customer requirements regarding the selection of sub-suppliers or incoming materials must be documented.
- Interface agreements are available when required (designated) suppliers are agreed upon with the client.
Product / Process Development:
- Inquiry documents
- Contract documents
- Requirement specifications (product, process)
- Customer requirements
- Legal requirements
- Purchasing conditions
- QM specific requirements
- Quality agreements
- Requirements for documentation
- Logistics requirements (JIT, JIS, on consignment)
- Schedules, technical delivery conditions
- Access to portals Information platform in Internet
- Definition of responsibilities for suppliers (e.g., qualification, sample submissions, approval, testing…).
- Testing regulations
- Catalogue of characteristics / reference examples for decorative surfaces.
- Experience with previous projects
- Product /Process characteristics
- Order documents with item lists and schedules
- Laws / regulations
- Environmental aspects, re- cycling requirements
- Proof for capability
Product development:
- Specifications, technical drawings
- Special characteristics
Process development:
- Suitability of facilities, tools and testing equipment
- Layout of work and test facilities
- Handling, packaging, storage and identification
Planning of Product & Process Development (P3)
P3.2* | Can the manufacturing feasibility be evaluated according to the product and process requirements?
Minimum Requirements relevant for Assessment
Examples for Implementation
The procedure for evaluating the manufacturing feasibility must be regulated across divisions:
- All determined product and process specific requirements (technology, function, quality, logistics, software, …) must be checked for manufacturing feasibility.
- Material and personnel resources must be considered in the manufacturing feasibility study.
- The results of the manufacturing feasibility study must be available before tendering.
- The manufacturing feasibility of critical purchased parts must be ensured.
- If customer requirements cannot be fulfilled the customer must be notified or deviations “allowed” / approved from the customer (if the contract has been awarded).
Product / Process Development:
- Customer specifications and standards
- Dates, timeframes
- Regulations, standards, laws, environmental impact
- Requirements regarding product liability
- Buildings, premises
- CAM, CAQ
- Product / process innovation
- Inter-divisional manufacturing feasibility analysis
Process Development:
- Capacity monitoring
- Availability of incoming materials
- Manufacturing facilities, manufacturing sites
- Equipment, tools, production testing equipment, laboratory facilities, transport, container, storage
Planning of Product & Process Development (P3)
P3.3 | Are the activities for the product and process development planned in detail?
Minimum Requirements relevant for Assessment
Examples for Implementation
When planning the product and process development the level of detail is dependent on the component, software and complexity of the process:
- In the development phase, suitable methods must be used to secure the product and process development so that when the product goes into serial production it fulfils the operational conditions (function, reliability, safety, security). This must be considered in the planning.
- Risk analysis (Product and process FMEAs or similar methods) are part of the planning.
- New developments from products and processes should be taken into account at the planning stage
- At the planning stage, the development of new products and processes should take into account the requirements of the product operational conditions.
- The plans contain all information for product and process development (including dates and length of time, milestones within the overall project plan, production testing, PPA-date, Software standards).
- Methods for development release meet customer requirements and a clarified with the customer if deviations occur.
- Outsourced processes and services are part of the project planning.
Product / Process Development:
- Overall schedule or product and process development plan
- Customer requirements
- Layout inspection and functional verification plans
- Client schedule
- Lead times
- Deadlines for the procurement release, sup- plier approval and change stop
- Methods used to minimize risk (QFD, FMEA, statistical testing plan (e.g., DoE, Shainin, Taguchi)
- Detailed plans for proto- types / pre-production
- Regular status checks on the progress of the development (reviews)
- Project plans for investment items, (facilities and equipment).
- Logistics planning for all phases of the of product and process development including packaging
Product Development:
- Detailed planning for re- liability testing, functional testing, trial plan
- Deadline for development phase samples
Process Development:
- Deadlines for the production trial run, tool timing plans (off tool parts)
- Detailed planning for test plans, test equipment plan
Planning of Product & Process Development (P3)
P3.4 | Are the activities for customer support / customer satisfaction / customer service planned?
Minimum Requirements relevant for Assessment
Examples for Implementation
The customer requirements for the supply of parts are taken into account across the product life cycle:
- Concepts to continually ensure series supply including a safeguard for emergencies are provided in the planning phase.
- A fall-back concept is provided for product and process innovation.
- The analysis process for 0 km and field reclamation is planned for delivery. The customer requirements are taken into account for failure analysis.
- When introducing new technologies and products, the employee training, and the creation of the necessary infrastructure are provided also in customer service.
Product / Process Development:
- Training plan
- Qualification matrix
- Investment planning
- Process Development:
- Inspection Planning for standard and stress testing
- Triggering criteria are de- fined
- Handbook NTF process
- Concept for the supply of spare parts
- Emergency plans
Planning of Product & Process Development (P3)
P3.5 | Have the necessary resources been taken into account for the product and process development?
Minimum Requirements relevant for Assessment
Examples for Implementation
The process for determination of resource is implemented:
- Determination of resources refers to the availability of qualified personnel, budget, infrastructure such as Building, testing equipment (hardware and software), laboratory equipment, machinery and equipment, ….
- Capacity for the implementation of prototypes, proto- typing, pilot production, production testing and serial production must be planned and considered.
- The resource planning is regularly adapted to changes in the project; potential bottlenecks are to be considered.
Product / Process Development:
- CAx equipment
- Availability of qualified personnel for respective tasks
- Capacity planning for all re- sources
- Product Development:
- Test / Inspection / Laboratory equipment (internal and external)
Process Development:
- Production sites, tools, production and testing equipment
Carrying Out Product & Process Development (P4)
P4.1* | Are the actions from the plans implemented for product and process development?
Minimum Requirements relevant for Assessment
Examples for Implementation
The conditions defined in the development planning methods for product and process development are applied, so that after implementation in the series the findings fulfil the product conditions of use (function, reliability, safety):
- In the development phase a FMEA must be used to ensure that the product and the process comply with the requirements of the customer in terms of function, reliability etc. When carrying out the product FMEA the proposed manufacturing site for the production shall be included.
- Special characteristics are identified and noted in the relevant documents (FMEAs etc.) and there are measures to ensure them.
- In the overall plan, a test plan must be included for the components, assemblies, subassemblies, components, software and materials including manufacturing processes from prototype and pilot production.
- The out-sourced products and services are taken into account. The implementation of product and process development is ensured in the supply chain.
- The documentation of the findings from the prototype phase and the pre-production phase are available for reference in the serial phase.
- The requirements for the test equipment are defined and implemented.
Product / Process Development:
- Methods to minimize risk (QDF, FMEA)
- Statistical design of experiments (for example: DoE, Shainin, Taguchi…)
- Poka-Yoke Principles
Product Development:
- Testing planning
- Assembly test and system test
- A, B, C Samples
- Endurance Tests
- Environmental simulation testing (e.g. salt spray test)
Process Development:
- Control plan / inspection plan
Carrying Out Product & Process Development (P4)
P4.2 | Are human resources available and are they qualified to ensure the start of the series?
Minimum Requirements relevant for Assessment
Examples for Implementation
A general personnel plan must be available:
- Personnel must be qualified for the relevant tasks. This also applies to the staff of external service providers. Appropriate certification must be available.
- Needs assessments will be carried out regularly during product and process development with regard to possible emerging bottlenecks and additional requirements.
- Qualified personnel resources are available for the implementation of prototypes and samples. Human resources for pre-production, production start-up and serial production are planned and personnel are qualified in accordance with the project plan.
- Processes that have been outsourced have also been considered.
Product / Process Development:
- Customer requirements
- Requirements profile for the relevant position
- Determine the need for training
- Proof of training
- Knowledge of methods and foreign languages
Carrying Out Product & Process Development (P4)
P4.3 | Are the material resources available and suitable to ensure the start of the series?
Minimum Requirements relevant for Assessment
Examples for Implementation
A process to determine resources has been established:
- Resource determination refers to the availability of test equipment, laboratory equipment, machinery, equipment, and the utilization of machinery and equipment. Supporting processes must be considered.
- Within the resource determination the necessary infrastructure is taken into account.
- Regular needs assessment must be carried out during product and process development with regard to possible emerging bottlenecks and additional requirements.
- Material resources for the realization of prototypes and sample are available. Material resources for pre- production, series start and serial production is planned and provided in accordance with the project plan.
- Outsourced processes must be considered.
- The resources must be available with a suitable lead time before the start of customer’s serial production.
Product / Process Development:
- Customer requirements
- Technical interface to customer and suppliers
Product Development:
- Test planning
Process Development:
- Facility planning
- Facility layout
- Machinery and equipment planning
- Quantities and throughput times
- Transport routes
- Transport, containers, storage
- Capacity before series start (initial stock)
- Supporting processes for example from logistics und IT should be considered
Carrying Out Product & Process Development (P4)
P4.4* | Are the required approvals and releases for the product and process development available?
Minimum Requirements relevant for Assessment
Examples for Implementation
The releases and verification of suitability is confirmed for all the items, assemblies, software versions and out-sourced products and services in accordance development schedules:
- The material data is confirmed and released.
- The actions from the FMEA have been implemented and confirmed in their effectiveness.
- The (Production process and product approval) PPA must be available at production release. For products with integrated software an additional software test report is available.
- Reference parts from sampling must be kept for at least the time laid down in the customer requirements.
- The verification and validation of the product and process are ensured before the customer SOP.
Product / Process Development:
- Test reports, protocols
- Supporting documents for purchased parts / suppliers
- Sampling results
Product Development:
- Specifications, drawings, requirement specifications
- FMEA IMDS, REACH, RoHS
- Product testing (for example: installation inspection, function testing, endurance testing, environmental simulation
Prototypes
- Confirmation of conformity with legal requirements
- Development releases from customers.
Process development:
- Logistics concept (e.g., suitability of packaging through sample shipping)
- Proof of capability of special characteristics
- Capacity studies
- Tool approvals
Carrying Out Product & Process Development (P4)
P4.5 | Are the manufacturing and inspection specifications derived from the product and process development and are they implemented?
Minimum Requirements relevant for Assessment
Examples for Implementation
The manufacturing and inspection characteristics contain all characteristics from the product and process development (including special characteristics). These must take into account all the components, assemblies, subassemblies, parts, software and materials including manufacturing processes that are part of the product:
- Results of the risk analysis are considered.
- The specifications include information for product control, production process control, methods and response plans and corrective actions.
- Product audits and layout inspection and a functional verification plans are defined.
- The specifications must be available for all phases: prototype phase (if required by the customer), pre- series and series phase.
Product / Process Development & Product development:
- Risk analysis (FMEA, FTA etc.)
- Process control plan (proto- types pre-series)
Process Development:
- Risk analysis (FMEA, FTA etc.)
- Production control plan (pre- series, series)
- Product audit plan
- Inspection plan
- Response plan
- Layout inspection and functional verification plan
- Series release (first and last piece)
- Testing within the series
Carrying Out Product & Process Development (P4)
P4.6 | Is a production trial run carried out under series conditions for the series release?
Minimum Requirements relevant for Assessment
Examples for Implementation
A production trial run must be carried out in order to assess all production factors and influences at the appropriate time and make any necessary corrections:
- The production trial run has provided evidence that the quality capability of the entire production process is given under serial production conditions (tools, equipment, cycle time, personnel, manufacturing and inspection specifications, measuring and testing equipment …).
- Note: Depending on the time of the audit some parts of the relevant production test could still be at the planning stage!
- The question is not relevant for the product development!
Product / Process Development:
Process Development:
- Customer requirements
- Determination of minimum quantities (intended production rate and flexibility as agreed upon)
- Process capability study
- Measurement capability
- Equipment and infrastructure are ready for start of series (measurement reports)
- Personal concept for serial production
- Work/inspection instructions
- Production tests according to customer schedule
- Packaging requirements
Carrying Out Product & Process Development (P4)
P4.7* | Is there a controlled method for the product handover from development to serial production?
Minimum Requirements relevant for Assessment
Examples for Implementation
A process exists for transferring work results from the project to the production:
- For products with integrated software, the results of the development (including the intermediate results and their documentation) are documented.
- Prerequisite for project delivery is a successful internal PPA process. Prerequisite for a series delivery release is the successful customer approval. Resulting actions from internal and external releases are implemented on time.
- Proof of capability can be shown for all special characteristics.
- The human resources are available in accordance with the planning and are qualified.
- The material resources include buildings, test facilities, laboratory facilities, equipment, facilities, etc. These are available and have been released.
- Releases for volumes of procurement are available.
- Measures to safeguard the SOP are specified and introduced when necessary.
Product / Process Development:
- Customer requirements
- Handover protocols/ check- lists with handover criteria
- Acceptance reports
- Production control plan
- Inspection plans
- Part history
- A method has been determined to carry out failure analysis and to introduce corrective measures
- Production metrics such as OEE, rejects, …
- Experience from the on-going project
- Measurement capability
Supplier Management (P5)
P5.1 | Are only approved and quality-capable suppliers used?
Minimum Requirements relevant for Assessment
Examples for Implementation
It must be ensured in serial production that only approved suppliers are used. An evaluation of the qualification capability must be available:
- An analysis of the quality performance of existing suppliers has to be considered using defined criteria. Risks in the supply chain have been identified, evaluated and reduced using suitable measures (emergency strategy).
Defined and documented criteria are used for supplier selection:
- Evidence of a qualification programme for suppliers who did not meet the selection criteria
- Evaluation of the quality capability (QM- System, Process) for example self- assessment, audit results, supplier certificates
- Results of the potential analysis
Also applies to:
- Research and development suppliers / prototype suppliers
- Suppliers of intangible products such as software
- Suppliers of equipment, machinery, tools
- Service providers (e.g., sorting companies)
- External testing labs
- Suppliers in outsourced processes
Supplier Management (P5)
P5.2 | Are customer requirements taken into account in the supply chain?
Minimum Requirements relevant for Assessment
Examples for Implementation
The communication of customer requirements must be regulated and traceable:
- Customer requirements also include requirements from drawings, components, software or component specifications from QM agreements and other applicable standards.
- Likewise, change management has to be considered during serial production.
- Interfaces are identified and secured.
Transmission of requirements, tolerances, time schedule, process releases, releases, complaints etc. with ensuring change management:
- Interface Agreement
- QAA (quality assurance agreements)
- Legal, regulatory requirements
Supplier Management (P5)
P5.3 | Have target agreements for supplier performance been agreed upon and implemented?
Minimum Requirements relevant for Assessment
Examples for Implementation
Target agreements have been made with all suppliers throughout the supply chain for products and pro- cesses. These agreements have been verified and implemented:
- Supplier output must be checked and evaluated within a defined period.
- If deviations occur actions must be agreed upon and their implementation including deadlines are to be monitored.
Measurable targets for quality, delivery quantity (batches) punctuality, for example to: reduce the ppm rates within the 0-failure strategy:
- QM agreements including escalation mechanisms
- Avoidance of special trips
- Reduction of rejects
- Reduction of the work in progress inventory
Supplier Management (P5)
P5.4* | Are the necessary releases / approvals available for out sourced products and services?
Minimum Requirements relevant for Assessment
Examples for Implementation
A release must be available for all out-sourced products and services before serial production of new / changed products / processes:
- Unless otherwise specified, the supplier for the supply of modules has the full quality control responsibility for all individual components.
Specifications / standards / testing instructions:
- PPA-Reports when necessary with software test re- ports
- Proof of capability for special characteristics
- Legal / country specific requirements (e.g. CCC, Inmetro, IMDS, REACH)
- Qualification tests / reports
- Model releases
- Change management in the supply chain
- Approval agreements for the scope of small batches and individual requirements
Supplier Management (P5)
P5.5* | Is the quality of the out-sourced products and services ensured?
Minimum Requirements relevant for Assessment
Examples for Implementation
To monitor the quality of the out-sourced products and services, regular checks are carried out, documented and evaluated:
- Deviations from the supplier quality are processed through a standard complaint process.
- Layout inspection and functional verification checks are carried out according to customer requirements.
- Test, inspection and measurement equipment must be stored in an orderly manner and associated work- stations must be laid out appropriately (e.g., climate control, lighting order, cleanliness, and protection against damage and contamination).
Coordination of test / inspection procedures, processes and frequencies:
- Reference parts
- Sample size (e.g., Skip Lot)
- Evaluation of main failures
- ppm evaluations, 8D reports
- Agreement and tracking of improvement programmes
- Testing possibilities (internal and external laboratories and testing facilities, testing in accordance with ISO/IEC 17025) for raw materials (material certificates) and finished parts
- Gauges / fixtures
- Drawings / ordering and packaging requirements / specifications
- Proof of capability
- Layout inspection and a functional verification checks report
- Test certificates
Supplier Management (P5)
P5.6 | Are incoming goods stored appropriately?
Minimum Requirements relevant for Assessment
Examples for Implementation
Incoming materials and loading equipment must be stored in accordance with their release status so that they cannot be damaged or mixed:
- For materials that could be damaged by temperature, humidity, vibration, etc. and affect the quality of the final product, the transport and storage conditions must be defined and verified.
- Terms of transport should be determined for critical incoming materials.
- “Suspect” / quarantined products must be stored securely to prevent access to them.
- FIFO and batch traceability are to be ensured when the materials and goods are further processed.
- Material stock figures in the inventory control agree with the quantities actually in stock.
- Storage conditions conform with the product requirements.
Packing:
- Inventory control
- Labelling (traceability / test status / work sequence / use status)
- Quarantine stores; quarantine areas
- FIFO
- Batch-related use
- Shelf-life requirements
- Climatic conditions
- Protection against damage / contamination / corrosion
- Order and cleanliness
- Precautions to prevent mixing / mistakes
- Remaining quantities from production
Supplier Management (P5)
P5.7 | Are personnel qualified for their respective tasks and are responsibilities defined?
Minimum Requirements relevant for Assessment
Examples for Implementation
A description must be given of what responsibilities, tasks and authority the employees have in their relevant task areas (e.g., for incoming inspection, complaint processing, supplier management, supplier audit):
- Qualification requirements must be determined for each employee in relation to their tasks and qualifications carried out accordingly.
- Knowledge of previous complaints is available when appropriate for purchased products and services.
Product / specifications/ customer requirements:
- Knowledge about product features and production process for the individual parts of modules
- Standards / legislation
- Packaging requirements
- Assessment methods (audits, statistics)
- Quality procedures (e.g., 8D-method, cause / effect diagram
- Complaints and corrective action
- Qualification matrix
- Foreign languages
- Qualification of supplier auditors
Process Analysis & Production Control (P6)
P6.1 = What goes into the process? (Process input)
P6.1.1 | Has the project been transferred from development to serial production and is a reliable start guaranteed?
Minimum Requirements relevant for Assessment
Examples for Implementation
The project transfer to serial production has been carried out and if necessary unresolved issues are followed up on and implemented on schedule. The responsibilities for the entire handover process are regulated and acknowledged:
- A complete production process and product release including the documentation required must take place before the first production shipment.
- Measures are taken to secure the launch of production. A process for the further development of the process / product FMEA is defined and regulated.
- Tools, test and measurement equipment are available in the necessary quantities.
Project status reports:
- Transfer reports
- Milestone reports
- Defined actions with implementation schedule
- Process FMEA and actions
- Product FMEA and actions
- Production release report
- Machine and process capability examination
- Production test / production trial run and evidence
- Transport planning process
- Customer release (product release, process release)
- Nonconformity permission when necessary
- Released software standard
Process Analysis & Production Control (P6)
P6.1 = What goes into the process? (Process input)
P6.1.2 | Are the necessary quantities / production batch sizes of incoming materials available at the agreed upon time and at the correct storage / work-station?
Minimum Requirements relevant for Assessment
Examples for Implementation
The correct product (incoming material, part, component etc.) must be provided to the agreed quality, in the correct quantity and the correct packing, with the correct documentation, at the agreed time and at the agreed place. Parts/components must be available at defined storage areas/work-stations:
- At the workplace, parts and materials are provided as needed, taking into account the order quantity / lot size (for example, Kanban, Just in time, FIFO). Upstream processes are taken into account.
- After order completion, the return of unneeded parts (surplus) including their quantity is regulated.
- Sufficient and appropriate transport facilities
- Defined storage points
- KANBAN
- Just in time/ just in sequence
- Inventory control
- Change status
- Exchange of information to the return of unnecessary components / surplus
- Inventory
- Production levels tailored to the customer’s requirements
- Special requirements for components and containers (ESD-protection for electronic components, residue,)
Process Analysis & Production Control (P6)
P6.1 = What goes into the process? (Process input)
P6.1.3 | Are incoming materials stored appropriately and are the means of transport means / packing facilities suitable for the special characteristics of the incoming materials?
Minimum Requirements relevant for Assessment
Examples for Implementation
Packaging requirements must be consistently taken into account / implemented (also in the production stages):
- During manufacture and internal transport and also when being transported to and from service companies, suitable transport units must be used to protect the products from damage and contamination.
- Store areas /work-stations / containers must be appropriate for the tidiness and cleanliness required for the parts/products. Cleaning cycles are defined and monitored.
- The supply of parts/materials at the work-station/on the assembly line must allow for safe handling.
- Specified storage times and use-by dates for special materials/ parts must be monitored by appropriate methods (maximum and minimum storage times; specified interim storage times).
- Critical operating and auxiliary materials for plant and machinery with a direct effect on the product / product quality must be monitored accordingly.
- Parts / incoming materials / critical operating and auxiliary materials must be protected against environmental / climatic influences.
Stock quantities:
- Storage conditions
- Released special and standard transport containers
- Packaging requirements
- In-house transport containers
- Protection against damage
- Positioning of parts in the workplace
- Cleanliness, order
- Over-filling (bins and containers)
- Monitoring of storage times
Process Analysis & Production Control (P6)
P6.1 = What goes into the process? (Process input)
P6.1.4 | Are the necessary identifications / records / releases available and allocated appropriately to the incoming materials?
Minimum Requirements relevant for Assessment
Examples for Implementation
Released incoming materials must be clearly identified and recognizable. The release status must be identifiable and the release identification on bundles / batches/ load containers / parts must be defined:
- It must be ensured that only released materials/parts are forwarded to production/the next process stage and used.
- The traceability of the units produced must be ensured within a reasonable framework (e.g., documentation covering the use of batches).
- Depending on the product risk, traceability must be guaranteed across the entire process chain, from sub-supplier to the customer.
- Customer identification and traceability requirements must be taken into account.
- Legal and regulatory requirements are taken into account.
- The testing results of characteristics with special requirements for documentation and archiving are recorded accordingly.
Customer specifications:
- Customer requirements for labelling and tracing
- Legal requirements, product liability laws
- Identification of replacement parts
- Process for the release of released parts / materials
- Identification of released parts /materials (stickers, labels, issue slips)
- Records of approvals
- Traceability system or concept
- Documentation of special releases (number, duration, type of identification.)
Process Analysis & Production Control (P6)
P6.1 = What goes into the process? (Process input)
P6.1.5 | Are changes to the product or process in the course of serial production tracked and documented?
Minimum Requirements relevant for Assessment
Examples for Implementation
Change management must be clearly documented from the change request to implementation and responsibilities must be regulated:
- Changes that impact on customer requirements must be coordinated, approved and released by the customer. If necessary, a new PPA must be carried out. This includes both product and process changes (including software changes).
- Documentation of change status must be fully traceable.
- It must be ensured that, at all times, the correct design level of the incoming materials or software is used and the correct design level of the finished product is manufactured and shipped to the customer.
Change release by the organization and the customer (feasibility; interface to components, effect on costs and schedules.):
- Information about changes is passed onto process development, production are- as, stores or to sub- suppliers
- The level of implementation of the change is tracked (overview with status)
- Documented change record (part life history)
- Up-dating from documents involved (drawings, instructions)
- Up-dates of the FMEA (Product and Process)
- Verification and validation of changes including documentation
- Controlled introduction of changes and modified products / parts
- Lead times for changes, advance production of security stock before major changes which require a production stop (customer requirements etc.)
- Change levels of test/inspection equipment, gauges, tools and drawings
- Parameter changes
- Software
Process Analysis & Production Control (P6)
P6.2 = Work Content/ Process Sequence
P6.2.1 | Are the requirements of the control plan complete and have they been effectively implemented?
Minimum Requirements relevant for Assessment
Examples for Implementation
The production and test/inspection documents are complete and available and based on the production control plan. Inspection characteristics, facilities, methods, frequencies / cycles and re- qualifications must be defined:
- Access to these documents must be available at all times.
- Process parameters influencing product characteristics and/or quality must be fully stated. Tolerances must be given for process parameters and inspection characteristics.
- The control limits in process control charts must be defined, identifiable and traceable.
- Deviations and actions taken regarding process requirements and inspection characteristics must be documented.
- Required measures (action plan) for process disturbances are known and initiated and documented by the responsible employees.
- For products with specific requirements on the manufacturing process the appropriate data about machinery /tools /resources must be noted in the production control plan. When necessary these must also be recorded in the manufacturing and inspection documents.
- Conditions governing reworking are ensured and secured within the process (parts identification; re- checking/inspection, …).
Machine and process capability certification:
- Process parameters and tolerances (pressure, temperatures, times, speeds,)
- Inspection specifications (special characteristics, attributive characteristics, inspection specifications, methods and frequency)
- Data regarding machines/tools/ auxiliary aids (tool and ma- chine numbers)
- Guidelines regarding measurement fixtures/ reference points
- Work instructions including reworking
- Inspection instructions
- Specific requirements on the manufacturing technology, e.g., sampling relevant assignment of machines and plants
Process Analysis & Production Control (P6)
P6.2 = Work Content/ Process Sequence
P6.2.2* | Is there a repeat release of manufacturing processes?
Minimum Requirements relevant for Assessment
Examples for Implementation
The restart of production is the new release order for the start of production:
- Criteria for triggering a restart of production must be defined e.g., after an interruption of production.
- The restart of production is necessary for product and process and must be carried out and documented by authorised employees using acceptance criteria. Deviations and measures taken are to be documented.
- The restart of production inspection must be carried out using clear inspection instructions (quantity and method).
- If production is continued after collection of samples, parts should be considered suspect pending approval until the samples are approved.
- At the time of release the necessary reference and tolerance samples must be available.
Release of a batch:
- Release of reworked parts
- First piece release / first part release
- Tooling diagrams/ reference parts / installation parts (e.g., error check, red rabbit)
- Possible triggering criteria for a restart of production:
- Production interruption (e.g. night time in two shift operations, tool changes, material/ batch / product change
- Repair, tool change
- Setting data
Process Analysis & Production Control (P6)
P6.2 = Work Content/ Process Sequence
P6.2.3* | Are special characteristics managed in the production?
Minimum Requirements relevant for Assessment
Examples for Implementation
Special product characteristics and process parameters that affect the special characteristics are marked in the production control plan and systematically monitored:
- Records are maintained of non-compliances and corrective actions. Deviations affecting the characteristics of the product must be approved by the customer.
- Quality records are specified for significant characteristics (duration and type of archiving) and are coordinated with the customer.
Product FMEA / Process FMEA:
- Production control plan
- Quality records
- Statistical evaluations
- SPC evaluations
- Quality control charts
- Proof of capability (Cpk, Cmk, machine capability checks, …)
- Proof of inspection process
- Inspection results
- Drawings
- Special characteristics
Process Analysis & Production Control (P6)
P6.2 = Work Content/ Process Sequence
6.2.4* | Are non-approved and / or defective parts managed?
Minimum Requirements relevant for Assessment
Examples for Implementation
Non-approved parts, defective parts and/or parts with defective characteristics (scrap and parts for reworking) must be separated and collected or when necessary safely removed from the production process:
- These parts are to be either directly marked or marked on their container.
- Reworking criteria including testing are defined, known and implemented.
- Storage areas for blocked stock and restricted areas must be clearly labelled. Inadvertent use of restricted parts must be excluded.
- Setting masters, setup and reference parts must be labelled and protected against accidental use.
Labelling of scrap, rework and setting parts:
- Labelling of containers for scrap, rework and setting parts
- Defined scrap/rework stations in production
- Storage areas for blocked stock and restricted areas
- Records of rework and scrap
Process Analysis & Production Control (P6)
P6.2 = Work Content/ Process Sequence
6.2.5 | Is the flow of materials and parts secured against mixing / wrong items?
Minimum Requirements relevant for Assessment
Examples for Implementation
A mix of materials or the use of wrong materials, software or components cannot occur:
- Appropriate measures and checks must be taken to ensure the early detection and ejection or incorrectly installed items.
- Associated topics and actions must be included and examined in the Process FMEA and, if appropriate, in the Product FMEA.
- The process and/or inspection status must be clearly visible.
- The reuse of residues, separated parts, reworked parts, reusable parts from audits, inspected items etc. must be clearly defined (including regulations for traceability).
- Regulations for reintroducing parts or outsourced processed (e.g., sorting service) must be available.
Material and parts flow:
- Product / Process FMEA
- Poka Yoke actions
- Questioning and tests in production facilities
- Parts identification
- Identification of work, inspection and usage status
- Batch identification, traceability of the installation of batches or the production of batches
- Removal of invalid labelling
- Working papers with master data for parts / production
- Design status
- Material flow analysis
- Regulations for reworking
Process Analysis & Production Control (P6)
P6.3 = Process Support/ Personal Resources
P6.3.1* | Are the employees able to fulfil their given tasks?
Minimum Requirements relevant for Assessment
Examples for Implementation
A description of tasks with an appropriate job profile must be available for employees. A qualification programme (if necessary) is derived from this profile:
- Who is qualified for each task and activity must be documented?
- Trainings, instruction, briefings, / proof of qualifications that have been performed must be document- ed.
- Employees must be instructed in the handling and treatment of products with special characteristics.
- Suitable evidence of qualification for each activity must be present (e.g., forklift driving license, welding certificate, soldering certificate, vision test, hearing test).
- Employees responsible for measuring and testing must be trained in the correct use of measurement and testing equipment.
- Trainings / instructions are given at changes to the product / process and these are documented.
- The requirements also apply to internal and external temporary employees.
Training / qualification evidence:
- Qualification matrix
- Initial training plan with evidence
- Knowledge about the product and failures that have occurred
- Handling of measurement and testing equipment
- Training in work safety / environmental aspects
- Training in special characteristics
- Suitable evidence of qualification (e.g. welding certificate, vision test results, driving license for industrial trucks)
- Training about the product
Process Analysis & Production Control (P6)
P6.3 = Process Support/ Personal Resources
P6.3.2 | Do the employees know their responsibilities and authority in the monitoring of the product and process quality?
Minimum Requirements relevant for Assessment
Examples for Implementation
Responsibilities, duties and authority of the employees in their task areas are described and implemented (e.g., process release, first piece inspection, employee self-inspections, stopping the process):
- The employees know the consequences of faulty workmanship (which tasks / function the product has and what happens when they are no longer guaranteed due to faulty installation etc.).
- Employees receive regular information on the current standard of quality reached, both internally and with the customer (complaints).
- The requirements also apply to internal and external temporary employees.
Work / inspection instructions:
- Qualifications matrix
- Job descriptions
- Employee self-inspections
- Process release (setup re- lease, first piece inspection, last piece inspection)
- Process control (interpretation of control charts)
- Authority to stop and start the process
- Order and cleanliness
- Repair and maintenance is carried out or when necessary, arranged for
- Parts supply / storage
- Provision and adjustment of test / measurement is carried out or when necessary, arranged for
- Training about the product
- Quality information (target / actual values
- Product safety / product liability trainings
Process Analysis & Production Control (P6)
P6.3 = Process Support/ Personal Resources
P6.3.3 | Are the necessary personnel resources available?
Minimum Requirements relevant for Assessment
Examples for Implementation
The required number of qualified employees is avail- able for all shifts. Employee qualifications need to be considered when scheduling staff (e.g., qualification matrix):
- A scheme exists for supporting areas that are not continually in use (e.g., laboratory, measurement room).
- Fluctuations in on call staff and through absences (e.g., illness, holidays, training) are taken into account in the schedule.
- The requirements also apply to internal and external temporary employees.
Shift plan:
- Evidence of qualifications (qualification matrix)
- Documented absence management rules
- Workforce scheduling
Process Analysis & Production Control (P6)
P6.3 = Process Support/ Personal Resources
P6.3.3 | Are the necessary personnel resources available?
Minimum Requirements relevant for Assessment
Examples for Implementation
The required number of qualified employees is avail- able for all shifts. Employee qualifications need to be considered when scheduling staff (e.g., qualification matrix):
- A scheme exists for supporting areas that are not continually in use (e.g., laboratory, measurement room).
- Fluctuations in on call staff and through absences (e.g., illness, holidays, training) are taken into account in the schedule.
- The requirements also apply to internal and external temporary employees.
Shift plan:
- Evidence of qualifications (qualification matrix)
- Documented absence management rules
- Workforce scheduling
Process Analysis & Production Control (P6)
P6.4 = Material Resources
P6.4.1* | Can the product-specific requirements from the customer be met with the manufacturing equipment?
Minimum Requirements relevant for Assessment
Examples for Implementation
It must be shown that the processes are implemented in accordance with the customer requirements using the existing production facilities. Further it must be shown that the resulting products meet the customer specifications:
- The production facilities, machinery and equipment must be able to comply with the specified tolerances for the respective characteristic.
- Process capability must be determined for selected product and process characteristics and continually proven.
- The process capability must meet the customer requirements. For long term process capability, the minimum requirement of Cpk ≥ 1,33 must be met. In the case of significant characteristics where no capability level can be proven, 100% inspection is required.
- Layout and condition of the equipment, tools, fixtures and handling facilities meet the requirements under real production conditions.
Evidence of machine / process capability for special characteristics / process- determining parameters (e.g. pressure, time, temperature):
- Warning at deviations from limit specifications / parameters (e.g., an alarm, lamp, or automatic shut-down)
- Feed and removal systems
- Capability of replacement tools / reproducibility of fixtures, specifications
- Cleanliness requirements
Process Analysis & Production Control (P6)
P6.4 = Material Resources
P6.4.2 | Is the maintenance of the manufacturing equipment and tools controlled?
Minimum Requirements relevant for Assessment
Examples for Implementation
Maintenance activities (maintenance, inspection and repair) are determined and implemented for all installations, equipment and machines:
- Maintenance activities that have been carried out (scheduled and unplanned) are documented and analysed for improvement measures.
- A process for the analysis and optimization of down-time, machine utilization and tool life are implemented effectively.
- The key processes and critical machines are identified and appropriate maintenance activities (preventative or proactive) are carried out in terms of a risk- based maintenance programme. The availability of replacement parts must be ensured.
- Resources needed to carry out necessary maintenance measures are available.
- Tools undergo a tool management which includes the following:
- Status indication (OK / NOK/in repair)
- Tool identity card including all changes made to the tool
- Tool life (e.g., operating hours, strokes or shot numbers)
- Protection from damage
- Tool ownership
Availability / use of the appropriate technical documents:
- Maintenance plan / maintenance tasks
- Weak-point analysis
- Preventative tool exchange programme for units subject to increased wear and tear
- Storage and retrieval ma- chines / equipment for transport and storage etc.
- Availability of spare parts at production facilities producing key products
- Compliance with the pre- scribed maintenance intervals
- Documentation of maintenance activities
- Regular plausibility check of the scheduled maintenance intervals
- Hiring of external service companies to carry out maintenance
Process Analysis & Production Control (P6)
P6.4 = Material Resources
P6.4.3* | Can the quality requirements be effectively monitored with the measurement and testing facilities in use?
Minimum Requirements relevant for Assessment
Examples for Implementation
The test, inspection and measurement facilities used are suitable for the planned purpose and handling in production. They are included in the production control plan:
- Capability studies are carried out on the measurement devices and measurement systems employed. The accuracy of this equipment is appropriate for the purpose and for the characteristics to be checked.
- There is an identification system for measurement and inspection equipment. Administration of this equipment is based on the identification.
- A process for the periodic monitoring of measurement and inspection equipment is installed and implemented (responsibility for collection and return is defined). This process also takes into account the calibration of process-integrated measurement technology with an influence on the product characteristics.
- Measurement and inspection equipment accessories having an influence on measurement accuracy and the measurement result are monitored in the same way.
Production control plan:
- Measurement accuracy / capability of inspection equipment
- Proof of the capability of inspection processes
- Data collection and its evaluability
- Evidence of the calibration of inspection equipment
- Comparison of inspection equipment / measurement processes with the customer (e.g. inter-laboratory comparisons)
- Inspection stickers or certificates
- Reference component / set- up parts (e.g., Red Rabbit, error test pieces)
Process Analysis & Production Control (P6)
P6.4 = Material Resources
P6.4.4 | Are the work and inspection stations appropriate for the needs?
Minimum Requirements relevant for Assessment
Examples for Implementation
Conditions for the work-places and their surroundings are appropriate for the products and the work carried out, in order to prevent / eliminate contamination, damage, mixing-up of parts and misinterpretations:
- This also applies to permanent and temporary established rework, sorting and inspection stations.
- In addition, the work-place layout is adapted ergonomically to the work to be carried out.
Lighting:
- Cleanliness and tidiness
- Climate control
- Noise pollution
- Clean rooms
- Work place lay-out
- Surroundings / handling parts at the work-place
- Work safety
Process Analysis & Production Control (P6)
P6.4 = Material Resources
P6.4.5 | Are tools, equipment and testing equipment stored properly?
Minimum Requirements relevant for Assessment
Examples for Implementation
Tools, equipment and testing equipment (including gauges) must be stored and managed properly. This also applies for tools, equipment and test equipment not in use or not yet released:
- All tools, equipment and testing equipment are identified with their current status and all changes are documented (change history).
- Storage is provided where the equipment is protected against damage and environmental effects.
- Cleanliness and tidiness are ensured.
- The issue and use of this equipment are controlled and documented.
Stored free from damage:
- Cleanliness and tidiness
- Defined storage location
- Environmental influences
- Status identification
- Identification showing customer’s property, products/tools/devices provided on loan
- Defined release status and change level
- Storage and retrieval ma- chines / equipment for transport and storage
- Reference component / set- up parts (e.g. Red Rabbit, error test pieces)
Process Analysis & Production Control (P6)
P6.5 = Process Effectiveness
P6.5.1 | Are there targets set for the manufacturing process?
Minimum Requirements relevant for Assessment
Examples for Implementation
Process-specific targets are defined, monitored and communicated (quantities produced; quality metrics such as failure rates, audit results, through-times and process effectiveness figures (Cpk):
- Target requirements are coordinated and achievable; they are guaranteed to be up to date.
- Customer requirements are taken into account when setting targets.
- A regular comparison is made between specified and actual results.
Availability of installations and machines:
- Number of parts produced per unit of time
- Rework, scrap
- Production runs with no re- working, first passes, first time through quality, first pass yield
- Quality metrics (e.g., failure rates, audit results)
- Process metrics (process capability)
- Reduction of waste (e.g., scrap and rework, energy and process materials)
Process Analysis & Production Control (P6)
P6.5 = Process Effectiveness
P6.5.2 | Is quality and process data collected in a way that allows analysis?
Minimum Requirements relevant for Assessment
Examples for Implementation
To demonstrate compliance with the requirements and objectives which are needed for the evidence of product conformity, it is necessary to define and document quality and process parameters (target values) and record the actual data (actual value):
- It must be ensured that data can be evaluated.
- Special incidents are documented (shift / equipment book).
- The recorded data can be related to a product and process, the data is available, legible, accessible and archived as specified. Requirements for traceability are respected.
- The collected data is analysed and appropriate action for improvement is initiated. A risk-based approach is used here. The potential for improvement must be continuously determined from recent findings on quality, costs, services.
- Events that result in a change to the process or to the product must be documented in the appropriate FMEA and the respective measures taken are recorded.
Defect frequency cards:
- Control charts
- Special characteristics
- Process parameters (temperature, time, pressure….)
- Factory data collection
- Fault signals (e.g., plant standstill, power failure, programme error message)
- Parameter changes
- Error type / error frequencies
- Error costs (nonconformity)
- Rejects / reworking
- Blocking message / sorting actions
- Cycle times; through-put times
- SPC
- Pareto analyses
- Cause & effect diagrams
- Risk analysis (FMEA, FTA)
- Traceability system
Process Analysis & Production Control (P6)
P6.5 = Process Effectiveness
P6.5.3 | In the case of deviations from product and process requirements, are the causes analyzed and the corrective actions checked for effectiveness?
Minimum Requirements relevant for Assessment
Examples for Implementation
If deviations from product and process requirements occur, immediate containment actions must be taken to comply with the requirements, until the causes of failure are eliminated and evidence has been provided of the effectiveness of the corrective actions:
- These actions are known by the employees. Suitable methods for root cause analysis are in use.
- Corrective measures are derived, their implementation is monitored and the effectiveness verified.
- Production control plan and FMEA are updated as needed.
- Nonconformities that affect the properties of the de- livered product are communicated to the customer.
8D method:
- Cause & effects diagram
- Taguchi, Shainin
- 5 W method
- FMEA / error analysis
- Process capability analysis
- Quality control circles
- Analytical assessment methods
- Information flow to the customer
- Product FMEA and process FMEA
- Waivers / special releases
- Additional dimensional material, functional and endurance checks and tests
Process Analysis & Production Control (P6)
P6.5 = Process Effectiveness
P6.5.4 | Are processes and products audited regularly?
Minimum Requirements relevant for Assessment
Examples for Implementation
The audit programmes for process and product audits are available and implemented. Customer requirements are taken into account:
- The process and product audits carried out are suit- able to identify specific risks and weak points and implement corrective measures.
- A root cause analysis is carried out when deviations occur. Corrective measures are derived, their implementation is monitored and the effectiveness is verified.
- Product audits are periodically carried out and documented. Scope of the audit is the end product and where necessary intermediate products. In the product audit specified characteristics are examined and tested according to previously defined specifications.
- Nonconformities that affect the properties of the delivered product are communicated to the customer.
Product and Process Audit:
- Specifications
- Special characteristics
- Audit programme for product and process audits including scheduled and event-based audits
- Frequency of audits
- Audit requirements
- Audit results, audit reports
- Auditor qualification
Process Audit:
- Process parameter / capability
Product Audit:
- Labelling, packaging
- Capacity of the test equipment
- Software version
Process Analysis & Production Control (P6)
P6.6 = What should Process Produce? (Process Output/ Process Result)
P6.6.1 | Do the quantities / production batch sizes match needs and are they systematically directed to the next process step?
Minimum Requirements relevant for Assessment
Examples for Implementation
Parts/components must be forwarded to defined storage/holding points using suitable means of transport. In this, attention must be paid to the order quantity/batch size so that only the required quantity of parts/materials is moved to the stipulated work- station:
- The current state of the component (OK parts, re- worked parts, scrap) must be evident from the label- ling (component, container). Varying change statuses of the component must be taken into account.
- It is ensured that a further processing / forwarding of NOK parts is not possible.
Adequate, appropriate means of transport:
- Defined storage points
- KANBAN
- Just in time / just in sequence
- Stores management
- Change status
- Production quantities tailored to the customer’s needs
- Special requirements for components and containers (ESD-protection for electronic components, residual dirt)
Process Analysis & Production Control (P6)
P6.6 = What should Process Produce? (Process Output/ Process Result)
P6.6.2 | Are products / components stored in an appropriate manner and are transport facilities / packing arrangements suitable for the special characteristics of the products / components?
Minimum Requirements relevant for Assessment
Examples for Implementation
The product / components must be protected from damage by suitable storage and packing:
- Internal and customer-specific packing instructions are available and implemented.
- Storage points/containers must meet essential requirements for cleanliness & tidiness.
- Specified storage times must be monitored (specified maximum, minimum and interim storage times).
- Parts must be protected against environmental and climatic influences during storage and processing.
- These requirements are valid for the handling within the production process as well as the delivery.
Protection from damage:
- Positioning of parts
- Cleanliness, tidiness, over- filling (storage points & containers)
- Monitoring of storage periods / quantities stored
- Environmental and climatic influences
- Internal and customer- specific packing instructions
- Customer specific packaging instructions (inc. packing supplied by the customer)
- Information on available stock levels
- Substitute packaging
- Requirements for cleaning packaging
- Sufficient amount of package materials
Process Analysis & Production Control (P6)
P6.6 = What should Process Produce? (Process Output/ Process Result)
P6.6.3 | Are the necessary records / releases documented?
Minimum Requirements relevant for Assessment
Examples for Implementation
The labelling of the release status on containers / batches / carriers / components must be specified:
- Released products / components must be clearly marked and the release status must be visible.
- Special releases and releases with deviation approvals must be traceable by appropriate identification and documentation. The documentation must cover the period and/or quantity of parts involved. These details are documented including the identification on the component / carrier.
- Customer requirements for the labelling of reworked parts must be implemented and documented (amount / quantity / labelling / part history / use). The traceability of units produced must be ensured.
- For archiving requirements and duration, the customer requirements are taken into account.
Customer specifications:
- Significant characteristics
- Customer’s identification requirements
- Customer’s requirements for archiving time limits
- Archiving requirements/ regulations (EDP, paper, fire protection, legibility, …)
- Last piece inspection
- Part history
- Identification of special releases
Process Analysis & Production Control (P6)
P6.6 = What should Process Produce? (Process Output/ Process Result)
P6.6.4* | Are the customer requirements met at the delivery of the final product?
Minimum Requirements relevant for Assessment
Examples for Implementation
The customer specific requirements of the final product (delivery reliability, quality goals, quality performance etc.) are known and monitored. If deviations occur, corrective actions are defined and implemented:
- Final products are shipped in accordance with the customer requirements (shipping audit etc.).
- The handling of supplied products is regulated and implemented.
- Customers should be informed of delivery stops which affect them and further procedure should be coordinated with them.
Quality agreements with the customer:
- Customer specific requirements
- Customer requirements for the identification of special characteristics
- The planning of the shipping audit
- Storage / recall processing / parts supply / shipping
- Target agreements
Customer Support / Customer Satisfaction / Service (P7)
P7.1 | Are all requirements related to QM System, Product and Process fulfilled?
Minimum Requirements relevant for Assessment
Examples for Implementation
The internal and customer specific requirements on the quality system are fulfilled:
- Layout inspection and a functional verification checks are carried out according to the customer requirements.
- The customer requirements for the supply of spare parts during and after the production phase must be implemented.
- Customer requirements for the return of parts and their recycling must be implemented.
Quality agreements with the customer:
- Layout inspection and a functional verification concept e.g., carried out product audits, function tests, endurance tests
- Inclusion of sub-supplier for the supply of spare parts
- Supply guarantee after serial production
- Certification of the QM system
Customer Support / Customer Satisfaction / Service (P7)
P7.2 | Is customer service guaranteed?
Minimum Requirements relevant for Assessment
Examples for Implementation
It must be ensured that competent contact personnel are available for the various areas in the customer’s organization. Communication is ensured in accordance with the customer specifications:
- The monitoring of the product in the field is ensured.
- Access to customer portals in accordance with the customer specific agreement is ensured.
Knowledge of the product application:
- Knowledge of problems with the product and complaints regarding the product or transport
- Implementation of new requirements
- Notification of improvement actions
- World-wide customer service
- Information from the customer by non-compliance with the requirements
Customer Support / Customer Satisfaction / Service (P7)
P7.3* | Is the supply of parts guaranteed?
Minimum Requirements relevant for Assessment
Examples for Implementation
Concepts to ensure supplies are available and up to date. These concepts should also cover emergency situations:
- For this, not only the in-house processes but also the processes or suppliers must be considered.
- Procedures must be in place which guarantees that the organization informs the customer immediately when supply shortages are detected.
- The information must include the expected duration and extent of the shortages and the actions which have been taken.
Contingency plans (e.g., for alternative production, sup- pliers, transport):
- Capacity and reaction time for sorting actions
- Use of external capacity
- Communication regarding supply shortages
- Regulations covering authority to make decisions / escalation paths when introducing special actions
- Blocking of parts
Customer Support / Customer Satisfaction / Service (P7)
P7.4* | If there are deviations from quality requirements, are failure analyses carried out and corrective actions implemented effectively?
Minimum Requirements relevant for Assessment
Examples for Implementation
A complaint process that meets the customer requirements (e.g., 8D) is used for 0 km and field com- plaints:
- Procedures for failure analysis are defined. The necessary human and material resources are available to ensure punctual processing. The customer has to be informed when deviations to the time limits coordinated occur.
- By field complaints a failure analysis is to be carried out according to customer requirements (e.g., VDA Volume Field Failure Analysis).
Process for processing complaints:
- 8D process
- Internal / external analysis facilities (laboratories, comprehensive testing facilities, personnel)
- Use of problem-solving methods
- Performance tests
- Flow of information to the customer by deviations
- Knowledge store, lessons learned
- Quality control loop
- FMEA
- Access to the necessary release documents (PPA etc.)
- Testing concept for defective parts in the field (standard test/ stress test/ NTF test)
- NTF guidelines
- Performance indicators for processing of complaints
Customer Support / Customer Satisfaction / Service (P7)
P7.5 | Are personnel qualified for the various tasks and are responsibilities defined?
Minimum Requirements relevant for Assessment
Examples for Implementation
It must be determined which responsibilities, duties and authorizations each employee has in their respective area of responsibility:
- Training needs must be determined individually and implemented for each person, depending on their tasks.
- The employees know the product and the consequences of faulty workmanship for the supply of parts and the quality of the final product.
Organizational chart:
- Evidence of knowledge of the product / specifications / customer requirements
- Standards / laws (product liability)
- Processing / use
- Failure analysis
- Evaluation methods (e.g., audits, statistics)
- Quality techniques (e.g., Pareto, 8D Method, cause and effect diagram, Ishikawa)
- Foreign language skills
Terms and Definitions
Terms
Definitions
CAM, Computer Aided Manufacturing
CAM refers to the IT support for control and monitoring of production equipment and processes.
Capability of Measurement Processes
The capability of measurement processes documents evidence that the measurement process used (device / apparatus, operator, environment, etc.) is suitable for a specific application.
CAQ, Computer Aided Quality Assurance
CAQ System is the generic term for IT systems that are specifically developed to support quality management processes.
CCC, China Compulsory Certificate
A valid certification system in the People’s Republic of China. Chinese safety certification system required for specified parts or system parts when they are imported or used within the Chinese market.
Cmk, Machine Capability Index
The machine capability shows how a ma- chine is performing in relation to the tolerance limits for variance (capability corrected for position). This is calculated using mathematical and statistical methods and only the short time variance (scattering) is considered.
Conflict Management
Conflict management is the containment and prevention of escalation due to conflicts of interest. It is about the systematic, deliberate and targeted approach to conflicts in audit situations.
Conformity Confirmation
Confirmation of compliance with the requirements; Unlike certification only the actual status is evaluated. An on-going monitoring programme does not take place.
Consignment
Storage for products which remain in the ownership of the supplier until removal by the customer but are however, already owned by the customer.
Control Chart
With the help of control charts the performance of processes is monitored and statistically significant non-random deviations can be detected. Control charts help to focus on the stability of a process.
Control Cycle
System which continuously compares its actual value with the desired value and can react to implement corrective changes.
Cpk, Capability Process Index
Statistical estimation of the result of a characteristic of a process that has been demonstrated to be controlled. A process is capable when the statistical parameters for variance and position in relationship to the set-point and tolerance values meet the given criteria.
Deviation Permit
Risk assessment of parts that do not meet the specifications. It is assessed whether the parts can still be used. The permit al- lows the use of components that do not meet all the required steps and release specifications.
A deviation permit / authorization can be granted only by authorized personnel and only in coordination with the customer. The deviation permit must be attached together with the action plan for the execution of the shortcomings of the PPF documentation. See PPF and deviation permit / authorisation.
DOE, Design of Experiments
The objective of this method is to vary factors that influence the process or the system experimentally to find an optimum (e.g. optimal combination of injector, mixture, etc. to achieve the most fuel efficient combustion possible), experimental design using statistical methods to maximize the use of information from the experiments carried out.
DOT, Department of Transportation
Department of Transportation in the USA. The DOT defines specific requirements for components and their labelling.
ECE, Economic Commission for Europe
Economic Commission for Europe within the United Nations. Sets standards requirements for components and related component labelling.
Embedded Software
Embedded software is a part of a technical system and fulfils functions of the system.
Error Test Pieces
Monitoring the identification of defective parts using a part with known deviations from the specification see red rabbit.
Feasibility Study
A feasibility study assesses at an early stage whether a requested product (part, component, modules, system, process) can be produced under series conditions to the specifications given.
FIFO, First in First out
FIFO refers to the method of using the oldest parts in stock before newer parts are used.
First Pass Yield
Percentage of results that are correct in the first process run and do not require reworking (corresponds to first-time-through quality, straight running)
FTTQ, First Time Through Quality
Percentage of results that are correct in the first process run and do not require reworking (corresponds to first-time-through quality, straight running)
FMEA, Failure Mode and Effects Analysis
The objective of an FMEA is the early identification of potential sources of error / weaknesses and mistakes. The consequences are evaluated in a methodical risk analysis that initiates prevention measures. The FMEA method prioritizes potential errors according to the criteria “importance for the customer” / “occurrence probability” / “detection probability”.
FTA, Fault Tree Analysis
The fault tree analysis is a method for risk analysis for equipment and systems.
IMDS, International Material Data System
The IMDS is the material data system of the automotive industry. All materials used in the manufacturing of vehicles are collected, maintained analyzed and archived within the IMDS. Through the use of the IMDS it is possible to fulfil the requirements of national and international standards, laws and regulations that are required by automotive manufactures and their suppliers.
JIS, Just In Sequence
Provision of parts with a large number of variants in the planned production sequence.
JIT, Just In Time
The provision of parts or materials to the location they are needed in the production at the time they are required.
KANBAN
Method for reducing material stock in the production by using demand control according to the pull principal.
Layout Inspection and Functional Inspection
A layout inspection and a functional verification to applicable customer engineering material and performance standards shall be performed for each product as specified in the control plans. Results shall be available for customer review.
MSA, Measurement System Analysis
Evaluates the test process suitability (capability of measuring instruments and measuring systems) based on the product specifications. MSA is described in a publication published by the AIAG, in addition there are company specific requirements for measurement system analysis.
Negotiation
The auditor uses discussion and questioning techniques such as active listening, giving feedback, summary, importance of body language and intercultural aspects.
NTF, No trouble found
NTF refers to the fact that a rejected part is analyzed (standard test and load test) and no deviations from the specifications are found. The part is considered OK according to the findings and the complaint could not be validated. The cause of the error could not be identified.
OEE, Overall Equipment Effectiveness/ Overall Equipment Efficiency
The OEE (Overall Equipment Effectiveness) is a measure of the effectiveness of a production system based on its availability factor, efficiency factor and quality factor.
Pareto Analysis
Using the Pareto analysis priorities can be identified and visualized. In a Pareto analysis the characteristics (e.g. error, defective components, etc.) are sorted by frequency or importance.
Parts History
All changes that have been made to a numbered part and the associated manufacturing process are documented in the part history.
Pilot Lot
Production of a component prior to series production.
Poka-Yoke Principle
System method for preventing mistakes.
Positioning Parts
Parts that are produced during the setup process or that are required for setting up the system (e.g. master-parts, red-rabbit). These parts are not suitable to be used by the customer.
PPA, Production Process and Product Approval
Release Procedure for series production (sampling), described in VDA Volume. 2
PPAP, Production Part Approval Process
The purpose of the PPAP is to determine whether the product complies with the de- sign documents and specification requirements. Also see: APQP; PPF.
PPM, Parts Per Million
Representation of the error component based on the number of 1 million produced or supplied parts.
Process Risk
All risks associated with the manufacturing process that could have an effect on the product quality. Deviations arising from the process and how they impact on the properties of the product.
Process Step
Defined production step or production process as part of the overall process for the production of a product (e.g., machining, painting, plastic injection molding.
Product Group
Similar products with a comparable manufacturing process.
Product Risk
Risk that a product deviates from the specifications and the possible resulting effects, e.g. to function, safety, installation.
Production Peak
The production peak is the number of units produced at maximal planned capacity.
Prototype
Sample for or functional tests and reliability tests.
QFD, Quality Function Deployment
QFD is a quality tool developed in Japan in the seventies. It is used to determine customer requirements and their direct implementation within the technical specifications. The methodological approach is based on a separation of the customer requirements (what) of the technical product features and functionality (how).
Quality Assurance Agreement
A written quality assurance agreement providing all quality assurance measures for future deliveries between customers and suppliers. In this way the obligations regarding the quality of supply are regulated.
Quality assurance agreements constitute a contractual agreement between customers and suppliers.
Red Rabbit
Monitoring of error testing using a part with defined deviations from the specifications.
Required Supplier
When an organization manufactures modules and must use parts from a supplier stipulated by the customer, then this supplier is a required supplier.
Risk
Risks must be anticipated and estimated (from their probability and extent of dam- age, often expressed in possible cost). Also to consider are the technical, economic, political and socio-cultural risks.
Risk Assessment
Risks must be anticipated and estimated (from probabilities of occurrence and amount of damage, often in terms of possible costs). To be considered are technical, economic, political and socio-cultural risks.
Shainin
Test-based method (named after Shainin) used to identify relevant factors through the use of different measurement methods and experiments.
Skip Lot
The method of sampling inspection in which some lots will be accepted within a group without examination if the results of the sampling tests at a specified number of immediately preceding lots, meet defined criteria.
SOP, Start of Production
Start of the serial production.
SPC, Statistical process control
Statistical process control, improved with the help of statistical methods, the quality of production and service processes.
Start of Production
The primary goal of the start of production phase is to convert a new product from the laboratory like conditions to a stable product series. This phase begins as soon as the integration of all product components in prototype is successful and ends with the ability to produce the desired quality and quantity.
Straight Run
Percentage of results that are correct in the first process run and do not require reworking (corresponds to first pass yield, first time through quality).
Sustainability
Sustainability in the business context includes the safeguard of requirements regarding environmental protection, occupational safety and social standards as well as long-term profit orientation.
Taguchi
Test-based method (named after Taguchi) that helps design robust systems, products and processes.
Validation
Validation is the uses of objective evidence to confirm that the requirements which define an intended use or application have been met.
VDA Maturity Level Assurance for New Parts
Continuous tracking of the maturity level of new parts in conjunction with an objective assessment of the product and production process maturity at agreed times during the product implementation process.
Verification
Verification is the use of objective evidence to confirm that specified requirements have been met.
Abbreviations
Abbreviations
Definitions
CAx
Computer-Aided x
EDP
Electronic Data Processing
IEC
International Electrotechnical Commission
inkl.
Inklusive
Inmetro / INMETRO
National Institute of Methodology, Standardization and Quality
ISO
International Organization for Standardization
IT
Information Technology
REACH
Registration, Evaluation, Authorization and Restriction of Chemicals
RoHS
Restriction of Hazardous Substances
SAE
Society of Automotive Engineers
VDA
German Automotive Industry Association

“Hey, I am Sachin Ramdurg, the founder of VDiversify.com.
I am an Engineer and Passionate Blogger with a mindset of Entrepreneurship. I have been experienced in Blogging for more than 15+ years and following as a youtuber along with blogging, online business ideas, affiliate marketing, and make money online ideas since 2012.
1 thought on “VDA 6.3 [PDF| VDA 6.3 Process Audit [2024] – Complete Guide”