FMEA stands for “Failure Mode Effective Analysis”. FMEA is one of the best risk assessment or risk analysis tool in the world. FMEA is considered as one of the most important tool in 5 core tools of quality including 8D analysis. FMEA analysis helps you find out the potential failures based on severity, occurrence, and detection, which in turn helps you plan for recommended action based on the RPN values of the potential failures.
The FMEA is also called by the following names:
- FMEA = Failure Mode and Effective Analysis
- FMEA = Failure Mode and Effects Analysis
- FMEA = Potential Failure Modes and Effects Analysis
- FMECA = Failure Modes, Effects, and Criticality Analysis
Recommended for reading: Guide to FMEA tool
According to ASQ.org, the quality definition of FMEA stands as, “FMEA process is a step-by-step approach for identifying all possible failures in a design, a manufacturing, or production, or assembly process, or a product or service. It is one of the most preferred common analysis tool that helps to identify the risks in designing or manufacturing, and enables you implement corrective actions in order to eliminate the risks in future.”
“Failure modes” means the ways, or modes, in which something might fail. Failures are any errors or defects, especially ones that affect the customer, and can be potential or actual. “Effects analysis” refers to studying the consequences of those failures.
Failures are prioritized according to how serious their consequences are, how frequently they occur, and how easily they can be detected. The purpose of the FMEA is to take actions to eliminate or reduce failures, starting with the highest-priority ones. Failure modes and effects analysis also documents current knowledge and actions about the risks of failures, for use in continuous improvement.

Contents
- 1 FMEA Template Free Download [PDF] [2023]:
- 2 History of FMEA
- 3 FMEA Analysis [2023] | FMEA Process | FMEA Means – A Complete Guide To FMEA
- 3.1 What does FMEA stands for?
- 3.2 History of FMEA Analysis Tool
- 3.3 What is FMEA?
- 3.4 What is FMEA Process? What are the Types of FMEA Analysis?
- 3.4.1 What is FFMEA?
- 3.4.2 What is DFMEA stands for?
- 3.4.3 What is PFMEA?
- 3.4.4 What is FMECA stands for?
- 3.4.5 Difference between FMECA and FMEA?
- 3.4.6 What is System FMEA?
- 3.4.7 What is Software FMEA?
- 3.4.8 What is Service FMEA?
- 3.4.9 What is Manufacturing FMEA?
- 3.4.10 What is FMEA-MSR?
- 3.4.11 What is DRBFM?
- 4 Steps to Perform FMEA
- 5 When to Use FMEA?
- 6 Ground Rules of FMEA
- 7 Benefits of FMEA
- 8 FMEA Procedure
- 8.1 Purpose of FMEA Procedure:
- 8.2 Objective of FMEA Procedure:
- 8.3 Scope of FMEA Procedure:
- 8.4 Responsibility of FMEA Procedure:
- 8.5 FMEA Clause Reference:
- 8.6 International Standards References for FMEA Procedure:
- 8.7 Process Inputs for FMEA Procedure:
- 8.8 Key Notes for FMEA Procedure:
- 8.9 Steps in Development of FMEA Procedure:
- 8.10 Steps for FMEA 4th edition implementation:
- 8.11 Key Terms of FMEA Format:
- 9 FMEA Severity Ranking Free Download [PDF] [2023]:
- 10 FMEA Occurrence Ranking Free Download [PDF] [2023]:
- 11 FMEA Detection Ranking Free Download [PDF] [2023]:
- 12 FMEA Examples Free Download [PDF] [2023]:
- 13 Basic Terms of FMEA:
- 14 Conclusion
FMEA Template Free Download [PDF] [2023]:
Download FMEA Template here:
History of FMEA
The journey of FMEA was all began in the late 1940s, where in the procedures for conducting FMECA were prescribed in US Military, which was later then revised in 1980s. You can see the actual full-fledged usage of FMEA was really started in 1960s by NASA in its various NASA’s space missions, namely, Apollo, Viking, Voyager, Magellan, Galileo, and Skylab. The civil aviation industry is the one which was an early adopter FMEA with the help of Society for Automotive Engineers (SAE), which was then published in 1967. This lead to the extensive use of FMEA in civil aviation and the aerospace industries.
It was in the 1970s, when the FMEA started its movement into the various industries all across the world. It was mid of 1970s, when the automotive industries began the use of FMEA. It was Ford Motor Company which introduced FMEA to the automotive industries after the Pinto Affair for Safety and Regulatory considerations.
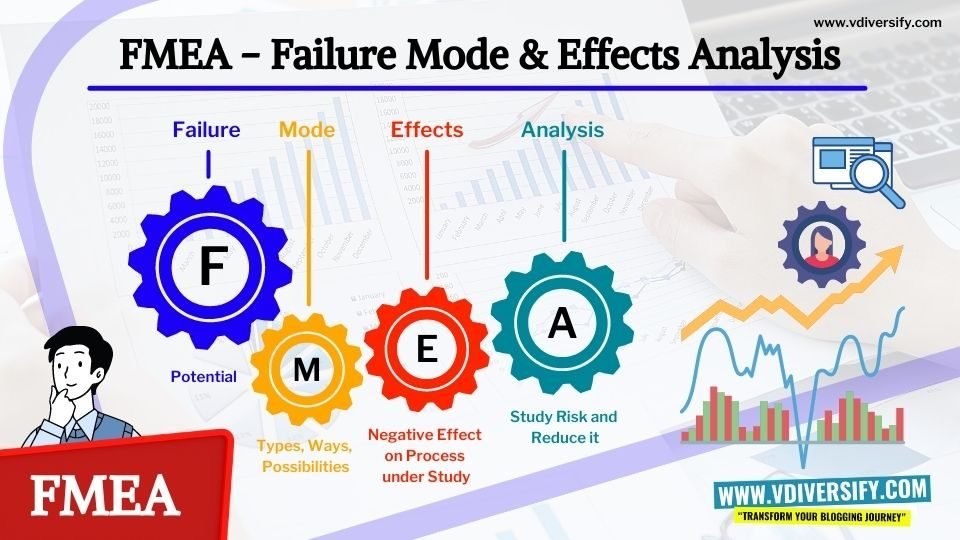
Ford applied the same approach in terms of Process Failure Modes and Effects Analysis (PFMEA) to identify potential failures and take corrective actions prior to moving into the production run. With the effective implementation of FMEA into automotive industry, the Automotive Industry Action Group (AIAG) first published an FMEA standard for the automotive industry in 1993.
The first edition of FMEA was published in 1994 by AIAG, and which now has revised into many editions. The last and latest version of FMEA was the fourth edition of FMEA which was also published by AIAG. In 2019, this fourth edition was replaced by the “New AIAG & VDA FMEA handbook” which covers both the requirements of AIAG as well as VDA standards. Not only that, it is also considered as a harmonization of the former FMEA standards of AIAG, VDA, SAE and other method descriptions, called as harmonized FMEA by VDA and AIAG.
Even though the FMEA was developed by the military for military operations, the FMEA process and methodology is now being used by many industries such as, semiconductor, automotive, software, food service, plastics, aviation, healthcare, and so on. With this, the Toyota has taken one step further by redesigning it with Design Review Based on Failure Mode (DRBFM) approach.
FMEA Analysis [2023] | FMEA Process | FMEA Means – A Complete Guide To FMEA
What does FMEA stands for?
FMEA stands for Failure Mode Effects Analysis. FMEA Analysis is a failure modes analysis tool which is used in the evaluation of any process both proactively and systematically for to identify where and how the processes might fail, thus by assessing the impacts of failure modes and to take the necessary actions to reduce the risks in the processes.
FMEA process is one of the tools of 5 core tools, which is used to find out the potential failure modes and accordingly put in controls so that the processes are streamlined. FMEA is one of the efficient tools of quality management to streamline the manufacturing processes. It is more effective and gives great results when combined with root cause analysis tool and 8D problem solving tool.
When you want to streamline any processes and want to find out the potential failures in the process, then you can use FMEA analysis tool. FMEA analysis is the most highly structured, systematic techniques for failure analysis.
FMEA is one of the tools which is now being used by many industries, organizations and businesses to find out the potential failure modes, root causes and implement controls along with actions to eliminate the failures prior to the physical running of the process.
History of FMEA Analysis Tool
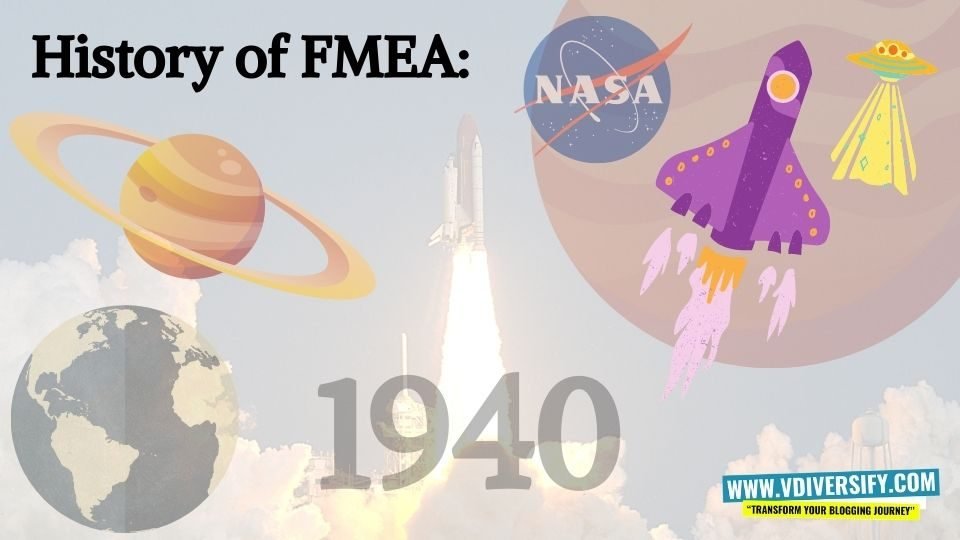
FMEA was first developed by the American Military almost at the end of the 1940’s. The main intention of developing Initial FMEA was to eliminate all the potential root causes as they were completely frustrated with munitions malfunctioning. Finally, a well detailed FMEA process was documented: MIL-P-1629.
As more and more organizations started using FMEA as a risk analysis tool, in 1993 the AIAG (Automotive Industry Action Group) has incorporated it into the QS9000 standard for automotive production and its suppliers. From then, the QS9000 became ISO/TS 16949:2008 and since November 2016, it is re-named as IATF 16949:2016.
To put it in simple words, the history of FMEA was as follows:
- US Military used FMEA in 1949
- NASA used FMEA in 1960s
- Auto Industry used FMEA in 1970s
- AIAG incorporated FMEA in 1982
- AIAG/VDA combined the FMEA in 2019
Sometimes the FMEA is extended to FMECA which is called as Failure Mode Effects and Criticality Analysis. This means the FMEA is extended to perform the criticality analysis, which is named as FMECA. FMEA is not a one man show. FMEA is conducted and prepared by Cross Functional Team (CFT) that includes all the process owners, key stakeholders or subject matter expertise along with operators.
What is FMEA?
FMEA means Failure Mode Effects Analysis which is also known as Potential Failure Mode Effective Analysis or Failure Modes, Effects and Criticality Analysis (FMECA). FMEA analysis is one of the 5 core tools of Quality Management which is one of the systematic methods for identifying possible potential failures that pose great risks in future for any process, product or service.
FMEA is a root cause analysis tool or a process analysis tool that helps to identify the following:
- Potential Failure Modes: One of the ways in which a product, a process or service can fail in future or in simple terms, potential possible defects
- Effects of Failure: What are the effects that are going to arise from the failure modes identified. In simple terms, the consequences of a particular mode of failure
- Cause of a Failure: One or many of the possible cause for an identified failure
- Analysis of the Failure Modes: Identification of Risk Priority Number (RPN) based on Frequency (F), Severity (S) and Detection (D)
What is FMEA Process? What are the Types of FMEA Analysis?
The full form of FMEA stands for failure modes and effects analysis. The FMEA is a forward logic or an inductive reasoning single point of failure analysis or risk analysis, which is considered as a core task in reliability engineering, safety engineering and quality engineering. A full-fledged, successful, and effective implementation of FMEA helps to identify potential failure modes based on the consideration of similar products and processes, or based on a common physics of failure logic.
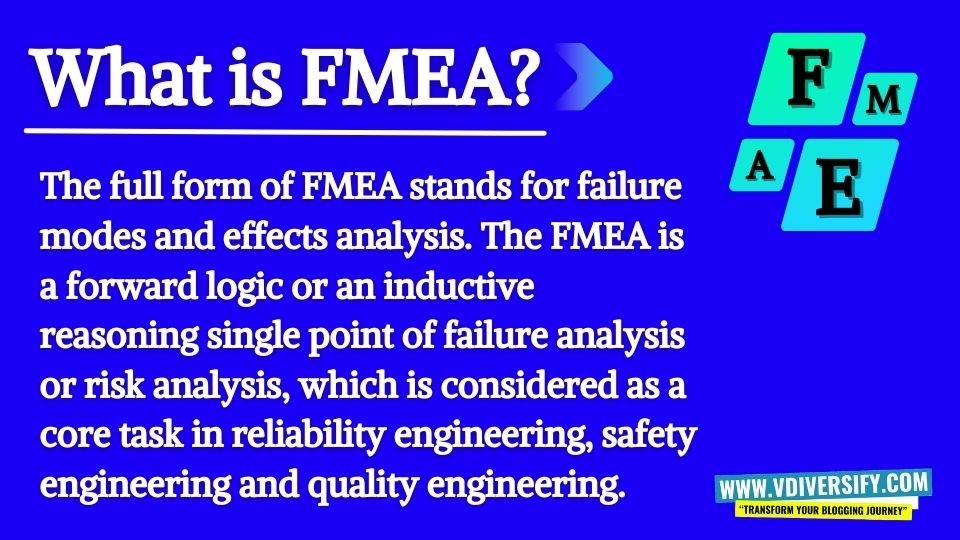
FMEA is used to structure mitigation for risk reduction based on either failure (or failure mode) effect severity reduction or based on lowering the probability of failure or both. The principle of FMEA is nothing but a full inductive and forward logic analysis, however the failure probability can only be estimated or reduced by understanding the failure mechanism. Hence, FMEA may include information on causes of failure (deductive analysis) to reduce the possibility of occurrence by eliminating identified (root) causes.
FMEA is an organized, systematic approach for assessing potential system failures and the consequences of those failures as part of results. The main objective of FMEA is to evaluate the risks associated against the identified failure effects and come up with a recommendation plan to detect, prevent, or mitigate those which are considered as critical with the highest risk priority numbers.
There are basically three types of FMEAs:
1. Functional FMEA (FFMEA)
2. Design FMEA (DFMEA)
3. Process FMEA (PFMEA)
Apart from this there are other multiple types of FMEAs and are mentioned as below:
- FMECA
- System FMEA
- Software FEMA
- Service FMEA
- Manufacturing FMEA
- FMEA-MSR
- DRBFM
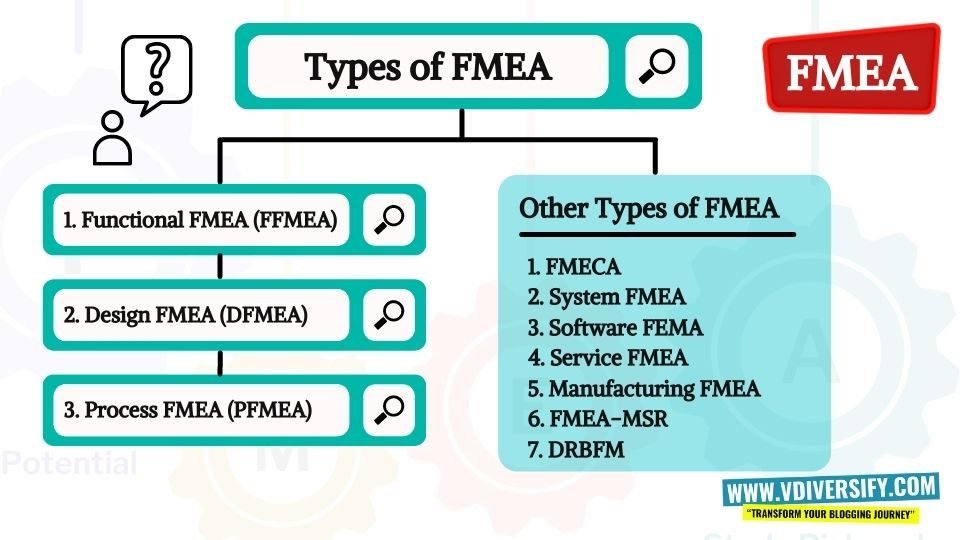
What is FFMEA?
FFMEA stands for Functional Failure Mode and Effects Analysis or Functional FMEA. The Functional FMEAs are sometimes referred to as System FMEAs. The functional FMEAs helps to analyze the functions of a system. This means, the functional FMEAs are used to analyze the functional requirements of a product or a process.
Functional analyses are needed as an input to determine correct failure modes, at all system levels, both for functional FMEA or piece-part (hardware) FMEA. The analysis should always be started by listing the functions that the design needs to fulfil. Functions are the starting point of a well done FMEA, and using functions as baseline provides the best yield of an FMEA.
What is DFMEA stands for?
DFMEA stands for Design Failure Mode and Effects Analysis or Design FMEA. DFMEAs allows you to assess, analyze, and address all potential failure modes during the early or end stage of product design. The DFMEA can be implemented in the hierarchy level or in terms of breakdowns in terms of all individual components of your product.
The main purpose of DFMEA is to ascertain and mitigate critical effects of failures prior to manufacture and deployment. Throughout the product life cycle of any product can be analyzed for its design and incorporate relevant changes by identifying potential failures and mitigate risks. The DFMEAs are performed on Products.
When you develop your DFMEA, it can be as much as detailed as you like. To give you an example, when you start your DFMEA at the initial stage or during the early stages of design phase which you can call it as preliminary DFMEA or proto-type DFMEA. And as and when the design starts maturing over the course of time, you can revise your DFMEA by break downing into critical lower level elements.
Steps to implement DFMEA:
1. Breakdown your system in a hierarchical format
2. Analyze the possible failure modes of each element in your system breakdown
3. Analyze the effects and causes of each failure
4. Rank the relative risk of each failure effect according to a criteria you prefer
5. Assign action items as needed to mitigate, eliminate, or detect high risk items
6. Go back and revise your risk levels based on completed actions
7. As your design matures, revisit your system breakdown to refine further and repeat steps 2 through 6
What is PFMEA?
PFMEA stands for Process Failure Mode and Effects Analysis or Process FMEA. The main purpose of the usage of PFMEA is to analyze and maintain process control objectives.
This means that, once you develop the DFMEA, you will identify the potential effects of failure during the manufacturing process or operations process and eliminate the risks by recommendation actions. Unlike the DFMEAs performed on products, the PFMEAs are performed on processes.
Steps to implement PFMEA:
1. Identify all potential failure modes of the process steps
2. Determine the resulting effects
3. Perform a risk assessment
4. Define a plan for recommended actions for risk mitigation
What is FMECA stands for?
FMECA stands for Failure Mode, Effects, and Criticality Analysis. It is one of the unique types of FMEAs that helps to incorporate a specific criticality analysis in to the FMEA. Usually, the FMECAs are performed based on the MIL-STD-1629A standard that defines a well-known and widely accepted procedure for FMEA.
Difference between FMECA and FMEA?
FMECA stands for “failure mode, effects, and criticality analysis (FMECA)” and FMEA stands for “failure mode and effects analysis (FMEA)”. FMECA and FMEA are best risk analysis tools that are widely used in various industries to identify and analyze the failure modes for processes and products. Even though they have most of the similarities between them, ideally they are not exactly the same.
FMECA has been built upon FMEA process by not only identifying potential failure modes. In fact it focuses on the topic of investigating and isolating any potential failure through a series of actions implementation. When compared to FMEA which assigns severity levels to various failures, the FMECA goes in more detail which helps to provide more accurate results, along with ranking those errors with the highest criticality number.
Before you conduct any criticality analysis actions initiation or implementation, the FMECA requires the application of FMEA. With this you can easily able to concentrate better on the most critical aspects, all thanks to the criticality analysis charts the probability of failure modes against the impact of the consequences. Similar to FMEA, FMECA can be used to help fulfil quality and safety requirements.
FMECA offers both qualitative and quantitative information, whereas the FMEA only offers qualitative information. This allows users to measure, a level of criticality to failure modes and order them according to importance. FMECA is usually conducted either with a top-down or a bottom-up approach.
What is System FMEA?
System FMEA is nothing but a Functional FMEA. The system FMEAs helps to analyze the functions of a system. This approach helps to list out all the functions that the design needs to fulfil.
What is Software FMEA?
Software FMEAs are the FMEAs that are widely used in the software industries. The Software FMEAs are performed by analyzing the ways that a software can fail and what is the impact or what are the resulting effects of those failures are on the system.
What is Service FMEA?
Service FMEAs are those types of FMEAs that are widely used in the service industries. Service FMEAs can be uniquely used in order to analyze a service that you are going to plan or intended to provide or intended to create that fulfils the customer needs and expectations.
What is Manufacturing FMEA?
As the name itself suggests, the manufacturing FMEAs are the ones that are used in the manufacturing industries. The manufacturing FMEAs are also called as process FMEAs that helps to identify the potential failure modes and effects of failure in all of the manufacturing processes.
What is FMEA-MSR?
The FMEA-MSR stands for Failure Mode and Effects Analysis – Monitoring and System Response or Monitoring and System Response FMEA. These are the FMEAs that are introduced in the New AIAG & VDA FMEA Handbook, which allows you to analyze how a product will fail when in use by the customer. The main purpose of FMEA-MSRs is to keep products safe or ensure that they remain in compliance with regulations.
What is DRBFM?
The DRBFM stands for Design Review Based on Failure Mode. It is a one step further approach in FMEA which was introduced and developed by Toyota Motor Corporation. The DRBFM was developed based on the philosophy that design problems occur when changes are made to existing engineering designs that have already been proven successful.
DRBFM methodology was developed by Tatsuhiko Yoshimura, a Quality Expert and a professor at Japan’s Kyushu University. Yoshimura knew that design problems occur when changes are made without the proper level of supporting documentation. Using the philosophy of preventative measures (Mizenboushi), he created his own philosophy of DRBFM.
The philosophy of DRBFM centers on three concepts:
1. Good design
2. Good discussion
3. Good dissection
The DRBFM methodology is now a recognized documented process by SAE (Society of Automotive Engineers) and also by AIAG (Automotive Industry Action Group).
Steps to Perform FMEA
FMEA is a systematic approach to identify potential failures and effects of failure. It should be followed as prescribed in the AIAG fourth edition FMEA manual or AIAG & VDA FMEA Handbook. It doesn’t matter what type of FMEA that you are going to perform, the steps to complete an FMEA remains the same across all FMEA types.
However, here are the common steps that one must follow to develop FMEA:
1. First, you break down your system, design, or process into its component elements – as granular or as high-level as you prefer.
2. From that point, you systematically go through each element and determine all the possible ways it can potentially fail.
3. For each failure, you analyze the effects and the likely causes of that failure.
4. You then proceed to rank each potential effect based on the risk criteria of your choosing. For example, you may consider such items as severity (how critical is it), its occurrence (how likely it is to occur), and detection (how likely it would detected). There are several standard methods to quantify risk level – such as RPN (Risk Priority Number) calculations that measure risk on a 1-1000 scale, and Criticality, which is a computed metric based on actual probability values. You can customize risk assessment criteria to best fit your needs.
5. Once the potential risk levels are ranked, you delve in to the important part of the analysis – determining how to minimize, detect, eliminate, or mitigate those you deem most critical. Typically, analysts then define a plan of recommended actions to implement in order to keep failure effect risks low.
6. You then go back and determine your revised risk levels based on completed action items to ensure you have met your risk goals.
When to Use FMEA?
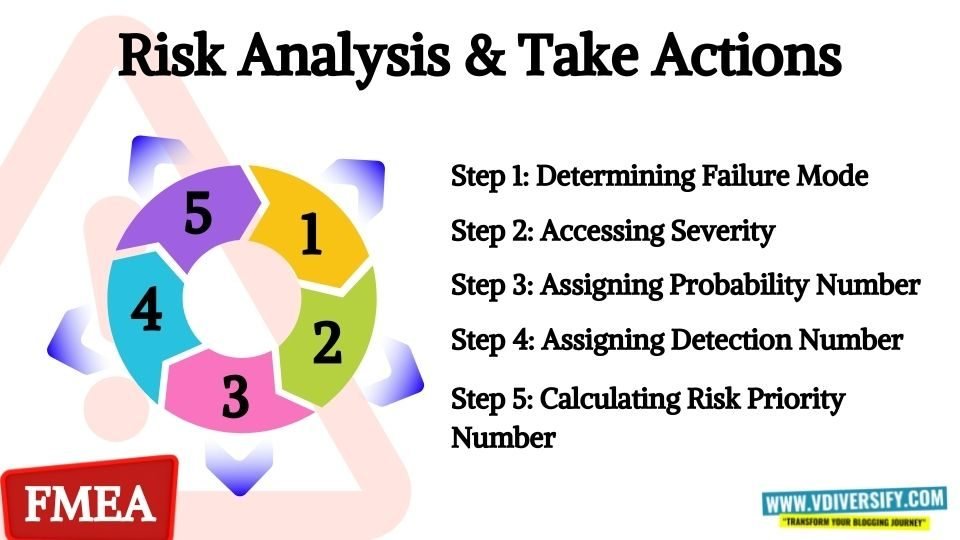
The use of FMEA can be done anywhere in the world for any process, product, or a service. However, you can use the FMEA in the following cases:
- When a process, product, or service is being designed or redesigned, after quality function deployment (QFD)
- When an existing process, product, or service is being applied in a new way
- Before developing control plans for a new or modified process
- When improvement goals are planned for an existing process, product, or service
- When analyzing failures of an existing process, product, or service
- Periodically throughout the life of the process, product, or service
Ground Rules of FMEA
The ground rules of FMEA for each of the FMEA performed involves the following and are not limited to:
- A set of project selected procedures
- The assumptions on which the analysis is based on or performed on
- The hardware that has been included and excluded from the analysis
- The rationale of the exclusions
- Indenture level of the analysis
- The level in the hierarchy of the part to the sub-system, sub-system to the system, etc.
- The basic hardware status
- The criteria of the system
- The success of the mission
This means that the FMEA performing team should put forth all efforts to define all ground rules before the FMEA begins. As said earlier the ground rules are not limited to the above and can be expanded and clarified as the analysis proceeds.
When you perform a FMEA, a typical set of ground rules can be defined as follows:
1. Only one failure mode exists at a time.
2. All inputs (including software commands) to the item being analyzed are present and at nominal values.
3. All consumables are present in sufficient quantities.
4. Nominal power is available
Benefits of FMEA
When you implement a FMEA, the benefits can vary from industry to industry, or product to product, or process to process, or service to service. However, the majority of benefits that are derived from a well implemented FMEA can be as follows:
1. It provides a documented method for selecting a design with a high probability of successful operation and safety
2. A documented uniform method of assessing potential failure mechanisms, failure modes and their impact on system operation, resulting in a list of failure modes ranked according to the seriousness of their system impact and likelihood of occurrence
3. Early identification of single failure points (SFPS) and system interface problems, which may be critical to mission success and/or safety. They also provide a method of verifying that switching between redundant elements is not jeopardized by postulated single failures
4. An effective method for evaluating the effect of proposed changes to the design and/or operational procedures on mission success and safety
5. A basis for in-flight troubleshooting procedures and for locating performance monitoring and fault-detection devices.
6. Criteria for early planning of tests
FMEA Procedure
To help you begin with here we have covered the FMEA procedure which you can use as a reference. In developing this FMEA procedure, we have referred and considered AIAG’s fourth edition of FMEA, which stays same across all industries. However, do remember that, a FMEA procedure can vary from industry to industry depending on the requirements.
Purpose of FMEA Procedure:
To establish a documented procedure for undertaking Process / Design Failure Mode Effective Analysis (DFMEA/PFMEA) for manufacturing or development of parts at “Company Name”.
Objective of FMEA Procedure:
To identify the Products/Processes where modification to the design or the operating, inspection, or maintenance, etc. strategies may be required to reduce the Severity of the effect of specific failure modes. It can be performed to meet a variety of different objectives, like, to identify Weak Areas in the Design/Process, the Safety-Critical Components, or Critical Maintenance and Test Procedures.
Scope of FMEA Procedure:
This procedure is applicable for all kinds of products manufactured or undertaken for development and processes followed in manufacturing of the same.
Responsibility of FMEA Procedure:
The development of FMEA lies with the Cross-Functional Team (CFT Team) or Multi-disciplinary Team. The CFT may consists of all process owners from various functions or departments as applicable.
These departments could be quality, engineering or design, manufacturing, production or assembly, machine maintenance, tool maintenance, purchase, supply chain, stores, logistics, sales, marketing, project management or new product development, reliability, testing, finished goods or warehouse, customer support, etc.
FMEA Clause Reference:
The FMEA can be referred to multiple clauses from multiple standards and are listed as below:
- 8.3.3.3 and 8.3.1.1 clause of IAFT 16949:2016
- 6.1.1 and 8.5.1.1 clause of ISO 9001:2015
- 7.1 clause of ISO 13485:2016
International Standards References for FMEA Procedure:
- ISO 9001:2015
- IATF 16949:2016
- VDA 6.3
- ISO 13485:2016
- AIAG fourth edition FMEA manual
- New AIAG & VDA FMEA Handbook
Process Inputs for FMEA Procedure:
When it comes to the need of process inputs to develop FMEA, there are many which varies from industry to industry. However, we have covered few of the process inputs that are needed in the development of successful and effective FMEA.
Here are the process inputs:
- Process Flow Diagram (PFD) or Process Flow Chart (PFC)
- Drawings and Technical Specifications
- Customer Specific Requirements (CSR)
- AIAG FMEA Manual (4th Edition)
- AIAG & VDA-QMC’s Design FMEA & Process FMEA Handbook
- IATF 16949:2016 Manual
- ISO 9001:2015 Manual
- ISO 13485:2016 Manual
- Past Trouble Database Sheet (PTDB)
- Lessons Learnt
Key Notes for FMEA Procedure:
When you are developing an FMEA for any product or service, you are recommended to follow the below key notes in successful implementation of FMEA:
1. FMEA to be carried out in the following cases:
- New Product Development
- New Process Design
- New Design and Development Activities
- Any Changed in Part or Product’s Design or Process
2. Major scenarios when an FMEA needs to be revised or updated:
- Against every customer complaint
- As per FMEA updation plan
- Change in control plans, PFD’s
- Change in designs, processes, or parts
3. New failures and causes must be identified from the review of corrective action reports, concession and process capability indices and the control charts
4. New Failures and Causes must be identified from the review of corrective action reports, concession and process capability indices and the control charts:
- Historical Quality Data (Failure wise and Cause wise if available)
- Historical Customer Complaints
- Customer Return Reports
5. During the initial process of potential FMEA process, the responsible Team Leader/Champion is expected to directly and actively involve all representatives from all affected areas. These areas should include every area but not only limited to manufacturing, materials, and quality
Steps in Development of FMEA Procedure:
Steps for FMEA 4th edition implementation:
1. Assemble a cross-functional team or a multi-disciplinary team of people with diverse knowledge or subject matter expertise about the process, product or service, and customer needs. Functions often included are: design, manufacturing, quality, testing, reliability, maintenance, purchasing (and suppliers), sales, marketing (and customers), and customer service.
2. Identify the purpose of the FMEA. What is the purpose that you are going to develop this FMEA? Which type of processes or which type of products or which type of services.
3. Identify the scope of the FMEA. Is it for concept, system, design, process, or service? What are the boundaries? How detailed should we be? Use flowcharts to identify the scope and to make sure every team member understands it in detail.
4. Clearly define the responsibilities in the development of this FMEA. Even though CFT is responsible for the development of FMEA, ensure that all process owners and subject matter expertise are also involved and given the responsibilities.
5. List down all the clauses that are applicable that lead to the development of this FMEA. For example, if you are from automotive industry, then refer IATF 16949:2016 for the applicable clause, if you are from non-automotive industry, then refer ISO 9001:2015 for the applicable clause, if you are from healthcare industry, then refer ISO 13485:2016 for the applicable clause, and so on.
6. Make a list of all the process inputs that are required in the development of this FMEA. There could be various artefacts that are applicable in developing the FMEA which may vary from industry to industry.
7. Fill in the identifying information at the top of your FMEA form. And for the remaining steps ask for information that will go into the columns of the form.
8. Identify the functions of your scope. Ask, “What is the purpose of this system, design, process, or service? What do our customers expect it to do?” Name it with a verb followed by a noun. Usually one will break the scope into separate subsystems, items, parts, assemblies, or process steps and identify the function of each.
9. For each function, identify all the ways failure could happen. These are potential failure modes. If necessary, go back and rewrite the function with more detail to be sure the failure modes show a loss of that function.
10. For each failure mode, identify all the consequences on the system, related systems, process, related processes, product, service, customer, or regulations. These are potential effects of failure. Ask, “What does the customer experience because of this failure? What happens when this failure occurs?”
11. Determine how serious each effect is. This is the severity rating, or S. Severity is usually rated on a scale from 1 to 10, where 1 is insignificant and 10 is catastrophic. If a failure mode has more than one effect, write on the FMEA table only the highest severity rating for that failure mode.
12. For each failure mode, determine all the potential root causes. Use tools classified as cause analysis tools, as well as the best knowledge and experience of the team. List all possible causes for each failure mode on the FMEA form.
13. For each cause, determine the occurrence rating, or O. This rating estimates the probability of failure occurring for that reason during the lifetime of your scope. Occurrence is usually rated on a scale from 1 to 10, where 1 is extremely unlikely and 10 is inevitable. On the FMEA table, list the occurrence rating for each cause.
14. For each cause, identify current process controls. These are tests, procedures or mechanisms that you now have in place to keep failures from reaching the customer. These controls might prevent the cause from happening, reduce the likelihood that it will happen or detect failure after the cause has already happened but before the customer is affected.
15. For each control, determine the detection rating, or D. This rating estimates how well the controls can detect either the cause or its failure mode after they have happened but before the customer is affected. Detection is usually rated on a scale from 1 to 10, where 1 means the control is absolutely certain to detect the problem and 10 means the control is certain not to detect the problem (or no control exists). On the FMEA table, list the detection rating for each cause.
16. Optional for most industries: Ask, “Is this failure mode associated with a critical characteristic?” (Critical characteristics are measurements or indicators that reflect safety or compliance with government regulations and need special controls.) If so, a column labelled “Classification” receives a Y or N to show whether special controls are needed. Usually, critical characteristics have a severity of 9 or 10 and occurrence and detection ratings above 3.
17. Calculate the risk priority number, or RPN, which equals S × O × D. Also calculate Criticality by multiplying severity by occurrence, S × O. These numbers provide guidance for ranking potential failures in the order they should be addressed.
18. Identify recommended actions. These actions may be design or process changes to lower severity or occurrence. They may be additional controls to improve detection. Also note who is responsible for the actions and target completion dates.
19. As actions are completed, note results and the date on the FMEA form. Also, note new S, O, or D ratings and new RPNs.
Key Terms of FMEA Format:
As per the AIAG FMEA guidelines here are the key terms that comes across the FMEA format as per fourth edition of FMEA. It represents what data you need to fill in to complete the FMEA. You can refer the screenshot below to follow along the same. You can also consider these steps as the steps in the development of FMEA.
1. FMEA Number:
Enter the FMEA document number. The number shall be FMEA/Customer-xxxx etc. digits alpha-numeric in nature.
2. Part Name/Part Description:
Enter the name of part or the description of the part as per the drawing developed by you or as per the customer drawing. E.g.: Mounting Bracket.
3. Part Number:
Enter the part number as per the drawing developed by you or as per the customer drawing. E.g.: 113547.
4. Key Date:
Enter the initial FMEA due date, which should not exceed the scheduled SOP date. In case of supply organization, this date should not exceed the customer required Production Part Approval Process (PPAP) submission date. E.g.: 01.01.2022.
5. Product Group/Model:
Indicate the Product Group or Model Name as mentioned in the Customer Drawing or technical specification. E.g.: TATA Ace.
6. Process Responsibility/Key Contact:
Enter the section/department responsible for maintaining the process. In case of DFMEA mention Design responsible Person & in case of Process mention the name of Plant Head/QA Head. E.g.: Mr.ABC Kumar.
7. Prepared By:
Enter the name of the Team Leader who has prepared the FMEA and affix his signature. E.g.: Mr.XYZ Kumar.
8. FMEA Date:
Enter the date when the original FMEA was completed and the Revision Number and Revision Date as and when the FMEA undergoes revision. E.g.: 01.01.2022.
9. Core Team:
Enter the name of Team Members, their Department and Designation. If space provided is not sufficient, annex the details. E.g.: Mr.ABC, Mr.XYZ, Mr.LMN, Mr.APG.
10. Process:
Enter a simple description of the process of operation taken up for analysis. E.g.: Assembly, Welding, Sheet Metal, etc.
11. Process Requirement:
Enter simple end/output requirement of the process. A process may have more than one process requirement, list them separately.
12. Potential Failure Mode:
The manner in which the process could potentially fail to meet the process requirements (including the design intent). The assumption is that the failure could occur but may not necessarily occur (These are negative of the Process Requirement).
13. Potential Effect(s) of Failure:
It refers to the effects caused by the invalid mode. To describe the consequence according to the founded or experienced condition by the customers. Identify potential effects based on the following criteria:
- Next Operation (NO)
- Subsequent Operation (SO)
- Customer End (CE)
- End User (EU)
Apart from the above the other below criteria can also be used for determining potential effects of failure:
- Downstream Users (DU)
- Ultimate Customer (UC)
- Vehicle Operation (VO)
- Operator Safety (OS)
- Compliance with government regulations (C.Gov)
- Machines / Equipment (M/C.E)
For a Process FMEA, downstream users can include an assembly operation / plant, or a service (dealer) operation.
FMEA revision details should be maintained clearly below the document. It should contain revision no., revision date, revision summary (a brief description of revision change i.e., what is changed in the FMEA), and reason for change.
14. Severity (S):
Severity is the value associated with the most serious effect for a given failure mode. Severity is a relative ranking within the scope of the individual FMEA. The Severity may be internal or external. If the customer affected is internal, concerned section In-charge shall be consulted for severity estimation. The severity shall be estimated on a 1 to 10 scale as per FMEA 4th Edition Manual.
Severity rankings are derived from AIAG’s FMEA 4th edition manual. The severity ranking chart is shown below. While rating severity in FMEA’s only the below table should be referred as it is derived from the AIAG’s 4th Edition FMEA Manual, Chapter IV.
Table A: Suggested PFMEA Severity Evaluation Criteria [Severity (S) Ranking]
Reference: AIAG’s 4th Edition Manual, Chapter IV. Table Cr1 Suggested PFMEA Severity Evaluation Criteria.
FMEA Severity Ranking Free Download [PDF] [2023]:
Download FMEA Severity Ranking here:
15. Classification:
Indicate the classification of special characteristics by the use of Symbols < SC > = Special Characteristics, < CC > = Critical Characteristics, < TYP > = Typical, Major/Minor based on customer drawings, and other symbols as prescribed in customer drawings, for product characteristics, and process characteristics.
The same symbol should be specified for the identified special characteristics in PFC’s, control plans, drawings, and related technical documents. The above symbols are generic and during any customer specific requirement, we refer to customer specifications.
16. Potential Causes:
List to the extent possible, each and every conceivable failure causes assignable to each failure mode. Describe the cause in terms of something that can be corrected or can be controlled.
Assume all inputs are conforming to specification. Ambiguous phrases like operator error, machine malfunction, fixture problem, etc., should be avoided. List out first level causes like Man, Machine, Method, Material, Measurement and Mother Nature (6M’s/4M’s) etc. and write the root causes under each first level causes. Typical examples are low curing time, moisture present in the material, air pressure less, etc.
For failure which have no direct relation to a cause, a cause and effect diagram should be drawn and design of experiments to be considered to determine the effect of root causes.
While generating the causes, the potential failure only should be considered not the effects. Refer the historical quality records, to verify that all causes occurred are listed.
17. Occurrence (O):
Occurrence is how frequently the specific failure cause is projected to occur. The occurrence ranking has a meaning rather than a value. It is the only way to reduce the frequency by design change, process change or controlling cause or mechanism of failure mode.
Estimate the likelihood of the occurrence of a cause on a 1 to 10 scale as per FMEA 4th edition manual. Only occurrence resulting in the failure mode should be considered for ranking. Failure detecting measures should not be considered here. If available from a similar process, statistical data should be used to determine the occurrence ranking. In all other cases, subjective assessment can be made.
If process capability included value such as Cp and Cpk’s are available for the similar processes those can be considered.
Occurrence rankings are derived from AIAG’s FMEA 4th edition manual. The occurrence ranking chart is shown below. While rating occurrence in FMEA’s only the below table should be referred as it is derived from the AIAG’s 4th Edition FMEA Manual, Chapter IV.
Table B: Suggested PFMEA Occurrence Evaluation Criteria [Occurrence (O) Ranking]
Reference: AIAG’s 4th Edition Manual, Chapter IV. Table Cr2 Suggested PFMEA Occurrence Evaluation Criteria.
FMEA Occurrence Ranking Free Download [PDF] [2023]:
Download FMEA Occurrence Ranking here:
18. Current Process Control:
Enter the proposed or current control that detects the failure mode, should it occur, or prevent the failure mode from occurring.
The types of Control are:
Type-1: Prevent the cause or failure from occurring (e.g., Mistake Proofing/fool-proofing, Automation).
Type-2: Detect the cause mechanism and lead to corrective action (e.g., SPC charts, set up approvals).
Type-3: Detect the failure mode (e.g., 100% inspection at stage or during the subsequent operations).
19. Detection (D):
Detection is an assessment of the probability that the proposed type of controls listed under current control column will detect a cause or failure. The initial detection ranking is to be based on Type-2 or 3 controls.
Estimate the detection ranking on a 1 to 10 scale as per FMEA 4th edition manual. The controls such as control charts, 100% inspection, sampling done on statistical basis is a valid detection control and deserves low ranking. The low occurrence does not deserve low detection ranking. Random quality checks are unlikely to detect the existence of an isolated defect. Sampling done on a statistical basis is a valid detection.
For multiple controls where it is difficult to assess, the combined ranking is to be given. Detection rankings are derived from AIAG’s FMEA 4th edition manual. The detection ranking chart is shown below. While rating detection in FMEA’s only the below table should be referred as it is derived from the AIAG’s 4th Edition FMEA Manual, Chapter IV.
Table C: Suggested PFMEA Detection Evaluation Criteria [Detection (D) Ranking]
Reference: AIAG’s 4th Edition Manual, Chapter IV. Table Cr3 Suggested PFMEA Detection Evaluation Criteria.
FMEA Detection Ranking Free Download [PDF] [2023]:
Download FMEA Detection Ranking here:
20. Action Taken:
After an action has been taken, enters a brief description of the action taken and effective date.
21. Action Results:
After the corrective action taken, the team leader is to verify the action for implementation. Estimate and record the resulting ‘Severity’ (S), ‘Occurrence’ (O) and ‘Detection’ (D) rankings. Calculate the “Resulting RPN”. If no actions are taken, leave the related ranking columns blank.
All resulting RPN’s should be reviewed and if further action is considered necessary, repeat Step-22 to Step-23. The controls should be written against each causes listed in potential causes column. If no control on the causes then write “No Control”.
Determining Action Priorities:
- Once the team has completed the initial identification of failure modes and effects, causes and controls, including rankings for severity, occurrence and detection, they must decide if further efforts are needed to reduce the risk. Due to the inherent limitations on resources, time, technology, and other factors, they must choose how to best prioritize these efforts.
- The initial focus of the team should be oriented towards failure modes with Highest Severity Rankings. When the Severity is 9 or 10, it’s imperative that the team must ensure that the risk is addresses through existing design controls or recommended actions (as documented in the FMEA).
- For failure modes with Severities 8 or below the team should consider causes having highest occurrence or detection rankings. Its team’s responsibility to look at the information identified, decide upon an approach, and determine how to best prioritize the risk reduction efforts that best serve their organization and customers.
21. Risk Priority Number (RPN):
Risk Priority Number is Severity (>S) multiplies by Occurrence (O) and Detection (<D).
Thus, Risk Priority Number (RPN) = (>S) x (O) x (<D).
The RPN value will be lies in between 1 to 1000. For higher RPN’s, the team must undertake efforts to reduce the risks through corrective action(s). In general, regardless of the resultant RPN, special attention should be given when the severity of the potential failure effect is high.
Say for example, if the RPN target value is equal or goes beyond 100 (i.e. ≥ 100) then corrective actions are planned to reduce the risks based on RPN values. Recommended actions are planned and FMEA will be updated and revised accordingly. Re-ranking will be done in action results and re-RPN Value will be calculated and hence RPN will be reduced. If in case customer gives the target for RPN value, then the same will be adopted.
Also based on severity the below RPN target is used for FMEA revisions unless otherwise specified by the customer.
(Note: RPN for Severity = 8 or 9 can be adapted to the customer requirements (for instance, raised to 50 if customer requires only this and not 36).
22. Recommended Action(s):
After completion of the steps described above, the RPN’s are to be analysed in the form of pareto-charts to identify the priority areas for control.
Higher risk priority numbers generally requires immediate action, however, the severity ranking more than 8 are to be considered with high priority irrespective of the RPN value.
The following actions should be considered:
- To reduce the probability of occurrence, revisions in process controls are required.
- The actions recommended should be to prevent/eliminate the causes to reduce the occurrence ranking. The prevention techniques such as mistake proofing methodology, SPC methods and continuous improvement are to be considered.
- The intent of any recommended action is to reduce rankings in the following order: Severity, Occurrence, and Detection.
- Only a process revision can bring about a reduction in the severity ranking.
- Generally improving detection control is costly and ineffective for quality improvement.
- Increasing quality control inspection frequency is not a positive corrective action and should only be utilized as a temporary measure.
- Emphasis must be on preventing/reducing occurrence of a defect rather than detecting them.
- Recommend change to current control systems such as introduction of statistical process control and process improvements rather than random quality checks or inspection.
- If no action is recommended for a specific cause indicates by entering “NONE” in this column.
Here are few of approaches to reduce these are explained below:
- To reduce Severity (S) ranking: Only a design or process revision can bring about a reduction in the severity ranking.
- To reduce Occurrence (O) ranking: To reduce occurrence, process and design revisions may be required. A reduction in the occurrence ranking can be effected by removing or controlling one or more of the causes of the failure mode through a product or process design revision.
- To reduce Detection (D) ranking: The preferred method is the use of error/mistake proofing. A redesign of the detection methodology may result in a reduction of the detection ranking.
23. FMEA Management (FMEA Review and Updation):
- This document is a living document and should always reflect the latest revision level. This is to be reviewed whenever there is a change in process, modifications in controls, on identification of new failures and causes, when the process becomes unstable and/or incapable.
- Whenever FMEA is reviewed the concerned process related documents like control plans, operating instructions, setup instructions, maintenance work instructions, etc., are to be reviewed and updated if required.
- When the process is out of control or the product is failure, FMEA CFT should evaluate FMEA again, ensure whether existing control measure can poses all the failure or not and definitude resolving.
- Review and update the FMEA during each milestone of NPD.
- When any 4M Change, FMEA should be reviewed and approved.
- When any customer claims / warranty claims, exceptional in-house rejection & quality catastrophe.
- Once in 6 months if any of the above not happened.
FMEA Examples:
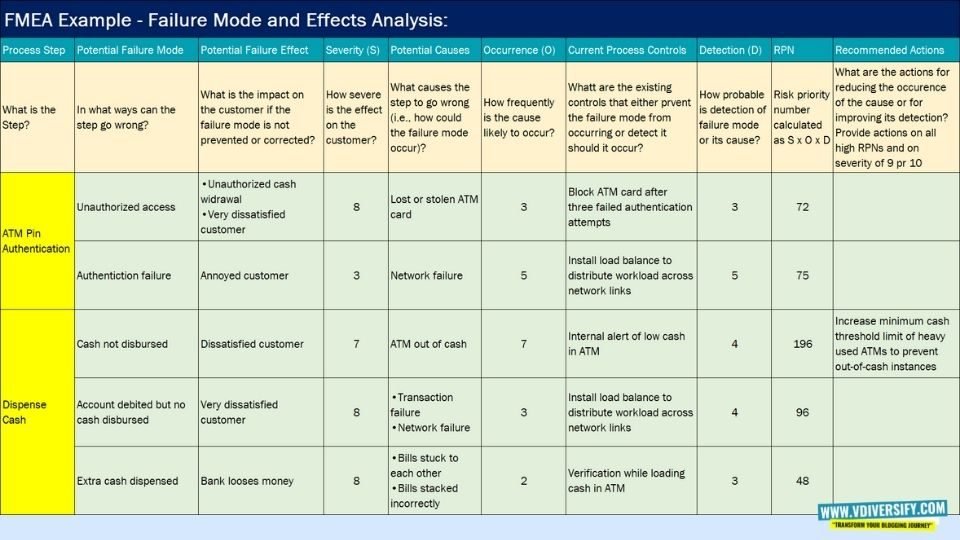
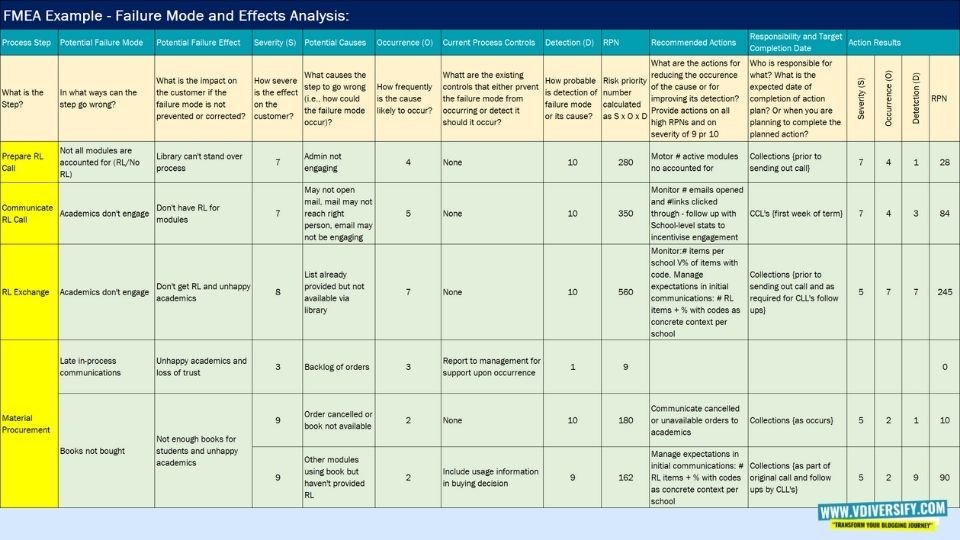
FMEA Examples Free Download [PDF] [2023]:
Download FMEA Examples here:
FMEA Template:

Process Outputs:
When it comes to the process outputs, you must capture all the relevant documents, templates, formats, or records including artefacts. These are the documents which have arrived after the completion of FMEA.
Here are the few of the process outputs:
- Updated FMEA sheet
- Risk priority numbers
- Recommended action plan
- Updated and improved severity, occurrence, and detection rankings
- Continual improvement programs
- Kaizens
- One point lessons
- Lessons learnt
Basic Terms of FMEA:
We have already gone through all kinds of key terminologies of FMEA. Now, let us understand and go through few of the basic FMEA terminologies:
Action Priority (AP):
The action priority is a new terminology that has been introduced in the New AIAG / VDA FMEA Handbook 2019. It replaced the former risk matrix and earlier terminology risk priority number which we have used in the AIAG’s 4th edition FMEA manual. It makes a statement about the need for additional improvement measures.
Failure:
The term failure represents the loss of a function under stated conditions.
Failure Mode:
The term failure mode represents a specific manner or way by which a failure occurs in terms of failure of the part, product, component, function, item, equipment, subsystem, or system under investigation. Depending upon the type of FMEA performed, failure mode may be described at various levels of detail such as at high level FMEA or low level FMEA.
Failure Cause and/or Mechanism:
Defects in requirements, design, process, quality control, handling or part application, which are the underlying cause or sequence of causes that initiate a process (mechanism) that leads to a failure mode over a certain time. A failure mode may have more causes.
Failure Effect:
Immediate consequences of a failure on operation, or the effects of failure, or more generally on the needs for the customer / user that should be fulfilled by the function but now is not, or not fully, fulfilled.
Indenture Levels (bill of material or functional breakdown):
An identifier for system level and thereby item complexity. Complexity increases as levels are closer to one.
Local Effect:
The failure effect as it applies to the item under analysis.
Next Higher Level Effect:
The failure effect as it applies at the next higher indenture level.
End Effect:
The failure effect at the highest indenture level or total system.
Detection:
The means of detection of the failure mode by maintainer, operator or built in detection system, including estimated dormancy period (if applicable)
Probability:
The likelihood of the failure occurring.
Risk Priority Number (RPN):
Severity (of the event) × probability (of the event occurring) × detection (probability that the event would not be detected before the user was aware of it)
Severity:
The consequences of a failure mode. Severity considers the worst potential consequence of a failure, determined by the degree of injury, property damage, system damage and/or time lost to repair the failure.
Remarks / Mitigation / Actions:
Additional info, including the proposed mitigation or actions used to lower a risk or justify a risk level or scenario.
Conclusion
FMEA is one of the best risk analysis tools out there in the world. No matter which industry that you are working and what kind of product you are going to develop, the FMEA analysis is the one that you must focus on.
The FMEA process helps you identify the potential failure modes, and effects of failure, which can be rated based on severity, occurrence, and detection to find out the risk priority number with respect to the current prevention and detection.
Later this risk priority number can be used to find out the recommended actions that helps to reduce the risk priority number again. In simple terms FMEA is the risk analysis tool that can be used to find out the risks in any product prior to its launch or production, identify the future failures, and take corrective actions way before so that you have a safe launch of your product to the market.

“Hey, I am Sachin Ramdurg, the founder of VDiversify.com.
I am an Engineer and Passionate Blogger with a mindset of Entrepreneurship. I have been experienced in Blogging for more than 15+ years and following as a youtuber along with blogging, online business ideas, affiliate marketing, and make money online ideas since 2012.
3 thoughts on “FMEA – What Is FMEA, Risk Analysis, FMEA Analysis, and 5 Core Tool [2023] – Best Quality Tool For Businesses”